When people hear the name Mel-O-Cream, they usually think of donuts. Founded in 1932 as a retail shop in Springfield, Ill, Mel-O-Cream International (www.mel-o-cream.com) manufactures bakery products, primarily for wholesale distribution to supermarkets and bakeries.
We currently offer a full line of quality frozen dough and pre-fried thaw-and-finish products. Mel-O-Cream produces more than 80 frozen donut items including specialty, seasonal and jumbo products. Since its debut in 1998, the number of items made on the pre-fried line has increased to more than 40. The pre-fried line makes items such as yeast raised, cake donuts, specialty donuts, and a selection of “Cake Donut of the Month” items. The list of products grows as customers’ needs change.
As donut manufacturing capacity and capabilities grew, so did the demands on our product packaging processes. Before this project, preprinted paper labels were manually glued to every case. The “best-if-used-by” date and batch code were also manually rubber-stamped to each case.
This scenario presented several operational issues. It required an extensive inventory of preprinted labels, and not having labels in inventory usually affected the production schedule. Manual label gluing and ink stamping were messy and labor-intensive tasks. For these and other reasons, we needed to automate our manual donut packaging system.
We’re familiar with the power and reliability of products from AutomationDirect (www.automationdirect.com) because we’ve used them on other projects. For this project, we chose a DL06 PLC, a GS2 variable frequency drive (VFD), a CoProcessor module with Extended BASIC interpreter, and an Ethernet Communications module—all supplied by AutomationDirect.
Automated Packaging Line Operation
We envisioned an automated packaging line that would do more than just eliminate the messy and labor-intensive gluing and stamping tasks. We needed a single application that would combine labeling, weighing, validating and diverting/routing of cases. Our solution had to be user-friendly, robust and reliable.
The best way for us to ensure that our solution would satisfy our requirements was to keep it simple with as few links in the chain as possible. We accomplished the design engineering, programming, fabrication, and installation in-house—enabling us to create the system exactly the way we wanted it.
We kept our design simple by having one Excel spreadsheet to hold all the data, including label information; one PLC to control all I/O and communications; and one simple PC-based Visual BASIC application developed in-house with no print drivers or Active-X controls.
At the end of the manufacturing process, the donuts are inspected for quality and bulk-packaged in corrugated shipping cases. Filled cases of two different heights are sent from the two production lines that merge into a single conveyor, which transports the cases to the labeling area. From there, they are counted, labeled, validated to ensure proper labeling, weighed, and routed to the appropriate palletizing area (Figure 1).
Automated Packaging Line Design Details
The automated packaging line doesn’t have a traditional HMI; instead, an external PC functions as an operator interface, which is driven by an in-house developed Visual BASIC program (Figure 2). In addition to the Visual BASIC program, the PC also runs the Excel application that contains the individual product data. Both programs interface directly with the label printer/applicator.
The “office type” PC is mounted inside a protective NEMA-4X panel along with the PLC and VFD. This enclosure, which is adjacent to the packaging/labeling conveyor, also supports the back of the label printer/applicator.
Print jobs are sent in ASCII from the Visual BASIC program running on the PC directly to the printer/applicator via an RS-232 serial port. The print jobs are not sent from the PLC. We tried printing from the PLC to the printer/applicator, which functioned well. However, outputting ASCII from the PLC became a daunting task because of our large ingredient legends.
There are only two case sizes that enter the labeling area, with one being taller than the other. Photoelectric sensors mounted at different heights identify which case is present. The packaging operator manually applies a special barcode label on the case whenever there is a batch change.
The PC-based Visual BASIC program increments the case count each time a case passes the photoelectric sensors. As a case passes its respective sensor, which is connected to a discrete input of the PLC, a bit is set in a PLC memory location. The Visual BASIC application running on the PC polls the PLC memory location via DirectNet to determine that a case has passed the sensor (Figure 3).
The PC displays the current batch number and case count, and then allows the operator to select the correct case label information to be printed. The Visual BASIC program provides UPC codes and target case weight to the automated packaging system. In addition to incrementing the case count, the Visual BASIC application also sends the appropriate label print job to the printer, which prints the label and applies it to the case.
The Visual BASIC program is tied to an Excel spreadsheet that contains all of the information to be printed on the label. Label information includes the product name, ingredient legend, UPC codes, best-if-used-by date, and net weight for every product code. There are more than 80 variations.
A scanner reads the barcode from the newly printed and applied label to begin the validation process. If the barcode data is incorrect or missing, the system rejects the case at the checkweigher station. If all is well, the case is weighed and the system compares the reading with the ideal weight for that product type.
The Excel spreadsheet contains the correct case weight and acceptable overweight tolerance. There is zero tolerance for underweight cases. The spreadsheet supplies this weight information to the Visual BASIC program, which writes these values to the PLC when the operator selects the product.
The PLC controls the checkweigher conveyor speed through the VFD. Another set of photoelectric sensors located directly before the checkweigher notifies the PLC that a case is approaching the weighing conveyor. Communicating with the VFD through Modbus, the PLC slows the conveyor speed to stop the case at the scale to obtain its static weight. Measuring static weight is much more accurate than measuring dynamic weight.
The checkweigher sends the case weight to the PLC in ASCII via conventional serial RS-232 connected to a CoProcessor module with the Extended BASIC interpreter. The PLC compares the scale weight to the target weight range, which is the target weight plus the overweight tolerance. If the case is within tolerance, the PLC tells the VFD via Modbus to restart the conveyor to transport the case off of the checkweigher.
A scanner, also connected to a CoProcessor module, reads the barcode of the labeled and weighed case. If the case is within tolerance, the PLC routes the case to the proper conveyor for palletizing by activating the appropriate conveyor diverter mechanism. If it’s out of tolerance, the PLC activates the same case rejection mechanism used to reject cases for incorrect barcode labels (Figure 4).
Small Footprint, Giant Capabilities
We’ve attempted to standardize on one PLC for our automation projects. We chose products from AutomationDirect because they’re very feature rich and extremely durable. Their small footprint PLC is a giant in its capabilities. Its communication capability, expansion slots, and a great selection of add-on cards make it a the perfect multitasking PLC for the majority of our automation projects.
We met our objective of designing a user-friendly and robust automated packaging and labeling system. We achieved a single solution that has performed with negligible downtime. We’ve printed and applied more than 7.5 million labels, and the system is still going strong.
Although learning the syntax of the DirectNet protocol was perhaps the most technically challenging aspect of this project, it was also the most rewarding. AutomationDirect’s Web site supplied technical documents, in particular a thorough breakdown of the DirectNet protocol. Knowing these details was critical to implementing the various communication interfaces on the project.
Through trial and error, we gained confidence reading and writing data to and from the PLC and the Visual BASIC program via DirectNet. The payback was a finished application that’s very efficient, compact and fast.
Albert Einstein said, “Make everything as simple as possible, but not simpler.” AutomationDirect caters to those who endeavor to control their applications with as much simplicity as possible. They’ve created a programming environment that supports users who seek high-level programming, yet accommodates users comfortable with lower level code such as mnemonics.
AutomationDirect provides a large inventory of products with fast delivery, long-term product-line support, a fantastic Web site and stellar documentation. The AutomationDirect knowledge base and user forum provide a wealth of information, and it was a source that we often referred to during this project.
How Mel-O-Cream Donuts are Made 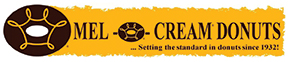
Mel-O-Cream Donuts International produces more than 80 varieties of donuts, all of which are shipped frozen. The process starts by placing the donut ingredients into mixers in the proper amounts as determined by weight.
The dough is mixed and delivered to dough feeders, which begin to manipulate the dough mass into a continuous ribbon. This ribbon of dough is sent by conveyor to a sheeter, which further rolls the dough into a thinner and wider sheet. While on the sheeter, rotary cutters cut the dough into the appropriate shape for sheet goods (rings, bismarks, long johns), or curled and cut the dough into cinnamon rolls or honey buns.
If the donuts are to be sold as frozen dough, they are sent to be flash-frozen in a spiral blast freezer. For pre-fried donut products, the raw dough pieces are transferred to the proofer to allow the dough rise.
The raised dough pieces are sent by conveyor to the tunnel fryer for cooking. The fried, hot donuts are allowed to cool on a spiral conveyor before transferring to the blast freezer.
Upon exiting the blast freezer, the frozen donuts are inspected for quality and bulk-packaged in corrugated shipping cases. The filled cases are conveyed to the labeling area to be counted, labeled, validated, weighed, and diverted to the proper palletizing conveyor.
By John Armstrong,
Director of Technology & Engineering,
Mel-O-Cream Donuts International Inc., Springfield, Ill.
Disclaimer: AutomationDirect does not guarantee the products described in this article are suitable for your particular application, nor do we assume any responsibility for your product/system design, installation, or operation.
Originally Posted: March 1, 2013