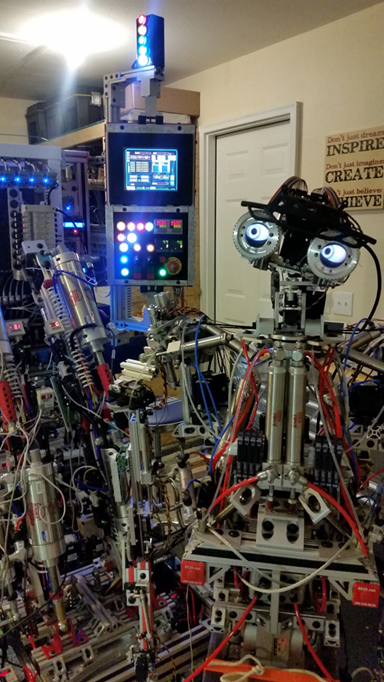
This home-built robot was created with industrial-grade automation technologies, providing a unique platform for learning career-enhancing skills.
Inspired by science fiction movies featuring robots like R2-D2 and WALL-E, Justin Flynn, a controls engineer, embarked on a journey to build a personal animatronic robot named Hubert Evolution 2 (HEV2), reminiscent of Johnny 5 from the 1986 movie Short Circuit. Industrial-grade automation technologies provided a robot-building learning experience that has translated into and supplemented the author’s career.
Today, Hubert stands seven feet tall and weighs about 1,000 pounds. He has expressive eyes and a wide variety of motion capabilities. The Automation.com July 2025 article titled Industrial Automation Brings Animatronic Robot Alive describes how Justin developed Hubert and learned a lot along the way.
Inspired Automation
The Hubert project began in 2006 and continued part-time until around 2020, spanning roughly 15 years of development. Justin, who gained technical training in the Air Force and college credits through Augusta State University, leveraged his skills and determination to undertake this massive project. The design started small, with a frame made from aluminum extrusions, and gradually expanded to include a movable torso, limbs, head, and other features.
For automation, he initially used consumer-grade hobby servos but soon graduated to using more capable control electronics, software, electro-mechanical hardware, and pneumatics, much of it industrial-grade commercial off-the-shelf (COTS) parts.
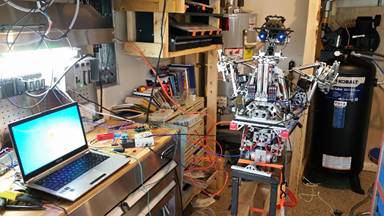
AutomationDirect played a crucial role in the project, providing a wide variety of automation and controls components. Justin relied on AutomationDirect’s technical information, support videos, and other resources to select components. The project involved continuous improvement, starting with small hobby servos and progressing to industrial-grade stepper motors and drives, AutomationDirect CLICK Koyo programmable logic controllers (PLCs), and ZIPLink pre-wired cables and connectors.
Industrial-Grade Tech
As the project progressed, the author incorporated pneumatics, linear pneumatic actuators, and Nitra valves to achieve motion. He learned programming along the way, some if it based on AutomationDirect online videos, and incorporated advanced algorithms, including proportional-integral (PI) control and time-proportioned loop control, to produce smooth and natural movement.
As development became more sophisticated, Justin moved up to the AutomationDirect Productivity3000 modular PLC combined with an AutomationDirect C-more human-machine interface (HMI) for user visualization and data/command entry.
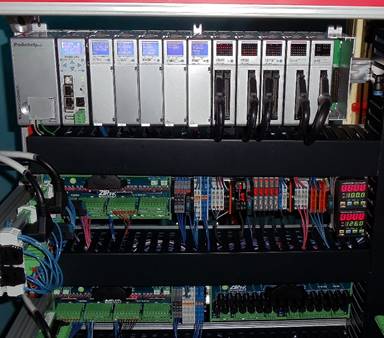
The project uses proportional-integral-derivative (PID) control, fuzzy logic, and various open-source controllers such as Arduino and Raspberry Pi microcontrollers. Although there are many smaller controllers, some of them using C++ and Python, the Productivity3000 serves as the main supervisory controller. Optical capabilities, speech recognition, and output hardware enable Hubert to interact with bystanders.
From Hobby to Career
For Justin, the Hubert project has been an excellent learning experience, with significant crossover to his professional job. Future plans for Hubert include updating the HMI, adding EtherNet/IP-controlled valve banks, and integrating a more advanced motion controller.
The ready accessibility and usability of AutomationDirect products have been foundational this project, and they make a great platform for anyone who is curious or aspires to innovate using automation technologies.
Justin hopes that Hubert inspires folks to create new projects of their own, opening up career and other opportunities. Check out the AutomationDirect website to learn about a variety of products that will help you with your next project.