To achieve the automation resilience needed for most industrial applications, a balanced combination of products and practices must be integrated.
Bill Dehner, technical marketing engineer for AutomationDirect, wrote an article for the May 2021 issue of Control Engineering titled Automation Built for Resiliency . Here’s a summary, click on the link above for the full text.
How many times have you had to reboot or repair a mobile device, a PC, or something even more important because of a malfunction? These types of failures are at the very least a nuisance. But for critical industrial systems, which are often expected to run 24×365, outages can result in far greater expenses and consequences.
Products and Practices
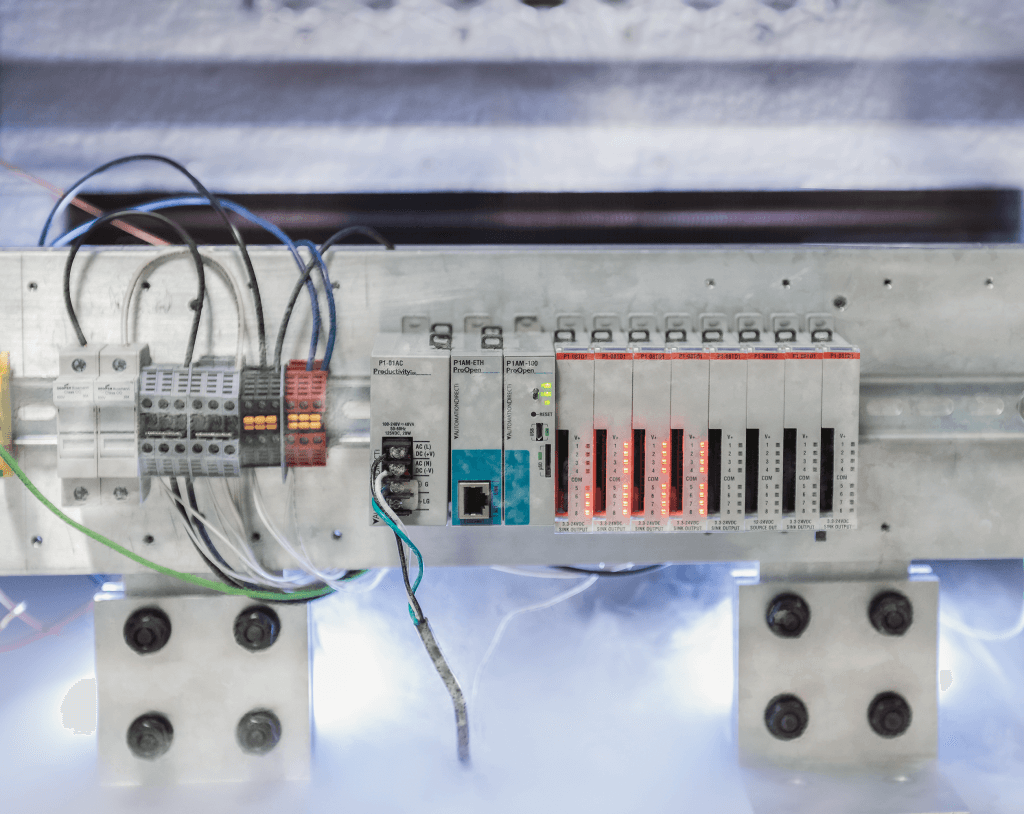
Automation systems are created from many unique—but closely related—elements such as sensors, wiring, power distribution, controllers, networks, software, and much more. Designers in the electrical, instrumentation, and controls (EIC) disciplines must choose the right combination to deliver functionality and resiliency, while keeping a close eye on cost.
Industrial Automation Products of All Types Must:
- Survive the environment they are subjected to.
- Carry all relevant certifications such as UL or American Bureau of Shipping (ABS).
- Be provided by reliable suppliers with a focus on testing under adverse conditions.
- Incorporate design features enabling them to excel for problematic applications.
Resiliency, Reliability, and Redundancy
Resilient systems are designed and built using highly reliable products, and in some cases by applying redundant configurations. Redundancy—the duplication of system elements to increase dependability—can be a key strategy, implemented in varying degrees for each part of an EIC system. However, redundancy is costly in terms of additional devices and implementation effort and is therefore not practical for many systems.
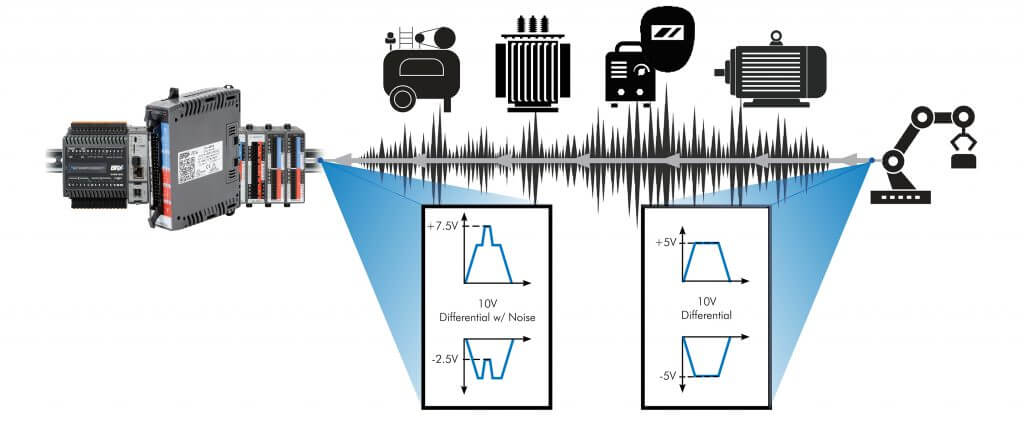
Electrical resiliency is created by using primary/secondary power sources, an uninterruptible power supply (UPS), and/or surge suppression. Installing digital communication and signaling cables separate from power, with good shielding or raceway protection is another step to improve resiliency.
Instrumentation resiliency is made possible by installing multiple instruments for critical measurements. For electrically noisy environments, a standard single-ended I/O module may not be the best choice, especially when a differential I/O version can effectively cancel out high EMI.
Controls resiliency involves many aspects. Some PLC platforms offer processor redundancy, which may not be warranted due to expense and complexity. But network redundancy, in the form of a self-healing ring, is often beneficial as the network is relatively exposed as it runs through a facility. For HMIs, a classic method of redundancy is simply adding more. However, a newer approach is to use “headless” HMIs, which can be accessed from anywhere via a mobile device.
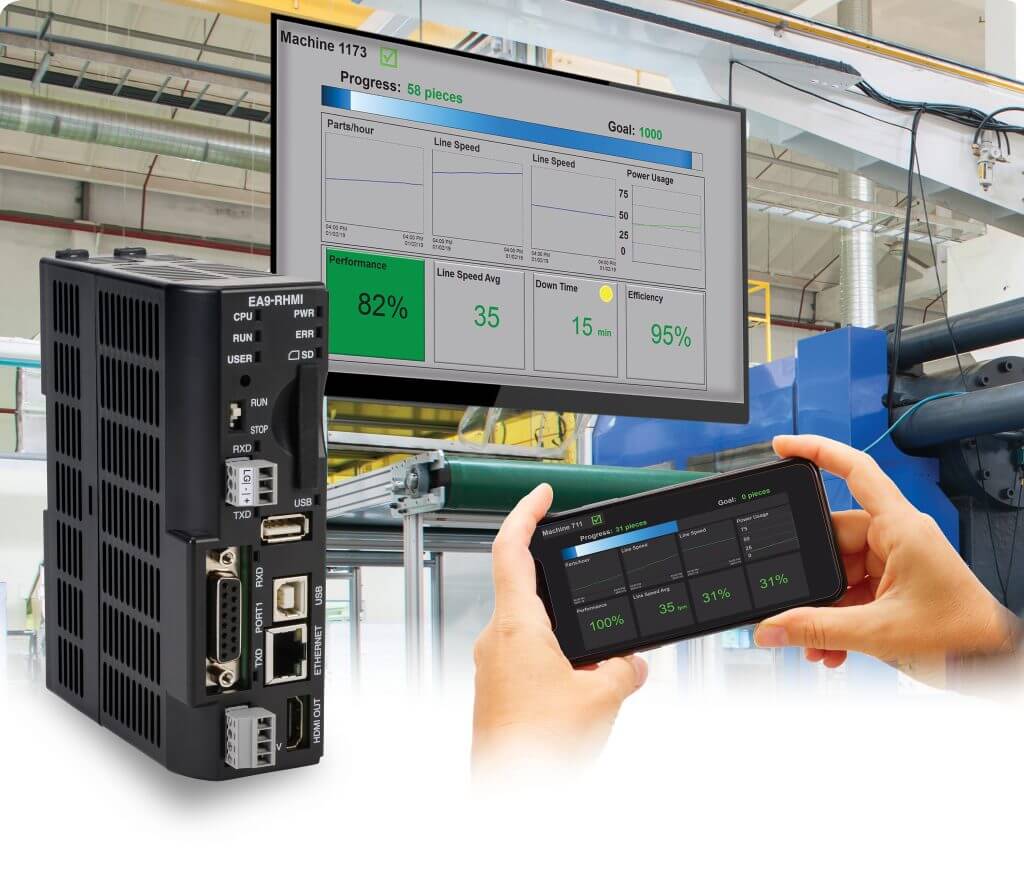
A Spectrum of Resiliency
Of course, a complete strategy for automation resilience considers many other factors such as good physical equipment designs and choosing proper motor and actuator products and control methods. Of special importance is ensuring good programming practices, which is a complex subject of its own.
The smallest and most economical projects can simply rely on solid products, installed properly following good basic practices. As equipment and systems grow in size, complexity, and criticality, there is greater opportunity to invest in more advanced electrical, instrumentation, and controls products and design practices to provide greater levels of system resiliency.