There are many practical and cost-effective ways for designers to incorporate automation redundancy for systems of any size.
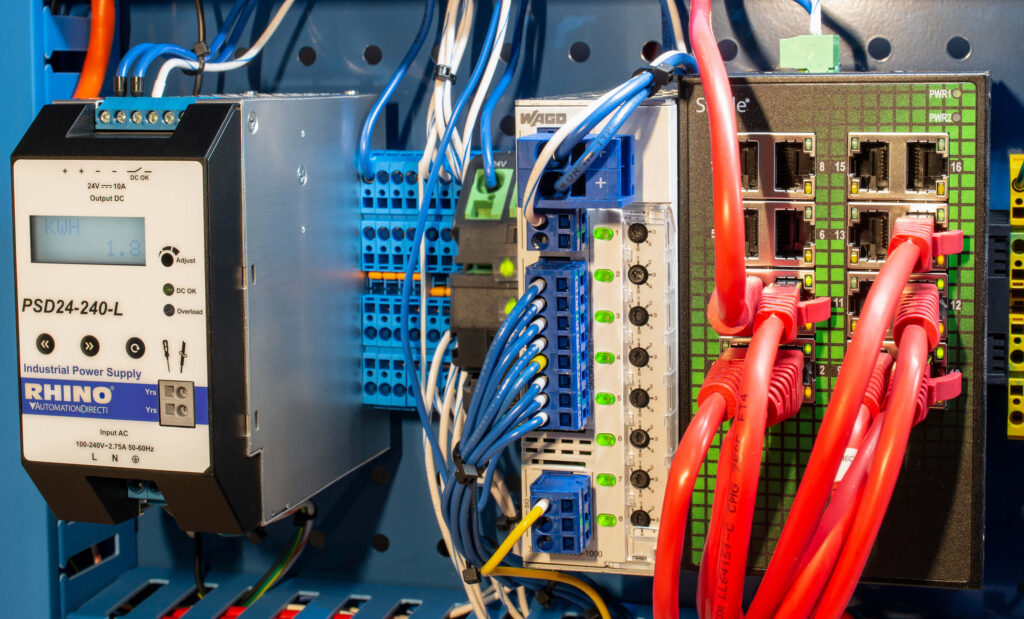
Automation redundancy has largely been reserved for larger process automation systems due to cost and complexity. However, there are now more products and design strategies suitable for applying redundancy to smaller-scale systems. Rin Irvin at AutomationDirect covers some of the options in his Control Engineering January/February 2024 article titled Think Redundantly About Automation Controllers Without High Costs. A video interview on the topic with Rin and CFE content manager David Miller is at Expert Interview Series: Rin Irvin, AutomationDirect.
Costly Conditions
Where possible, automation designers prefer to avoid single points of failure, which can lead to poor outcomes ranging from minor inconveniences to something much more serious.
A single point of failure is any electrical, mechanical, software or other element in a system which will cause the rest of the system to stop working as intended if it fails.
Redundancy is a way to overcome single points of failure, and it can be applied to:
- Power supplies
- Field instrumentation and sensors
- PLCs and hardwired control
- HMIs, SCADA, and other visualization systems
Among these items, PLCs are generally considered the most resistant to failure, but in all cases the risk of failure must be weighed against the cost to add redundancy to arrive at the most beneficial approach.
Redundancy Basic
The article considers a common example, which is a wastewater lift station using a VFD-driven pump and level instruments. Redundancy can be applied in several ways for such a system.
Power Supply
When only one utility power feed is available (which is usually the case), designers need to consider applying an uninterruptible power supply (UPS) or a battery control module to preserve control power. They can also incorporate dual power supplies combined with a diode module to preserve power if one supply fails. Electronic circuit breakers (ECBs) provide fast-acting circuit protection, and they can be monitored by a PLC and HMI/SCADA system.
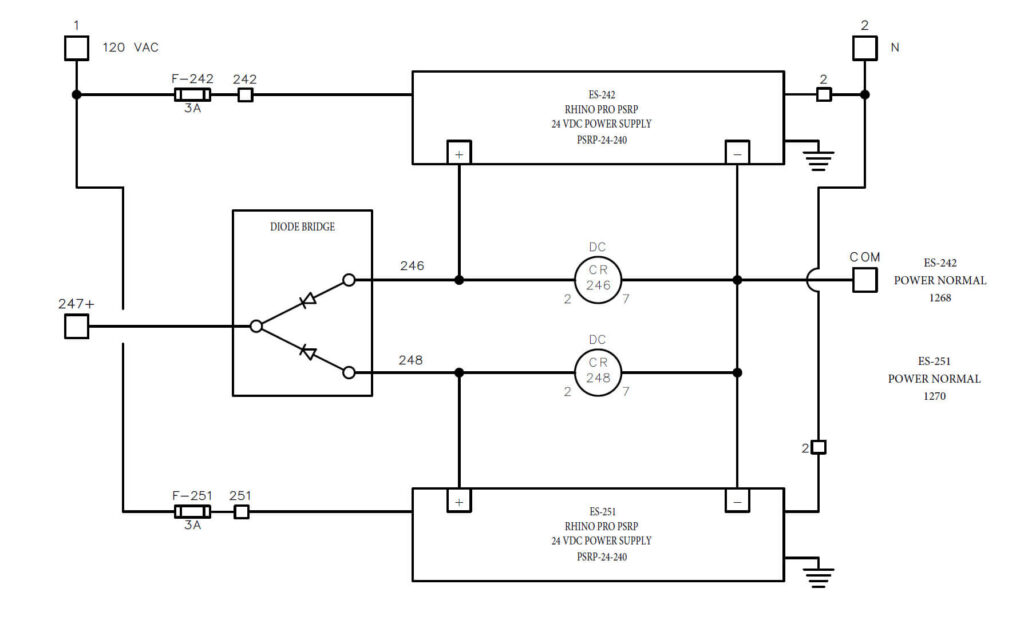
Sensors and Instrumentation
For critical measurements, especially under harsh conditions, designers should always consider implementing a second, or even a third, sensor, and use different technologies where possible. For level measurement, the wet well example could use a non-contact ultrasonic sensor as primary, a submersible hydrostatic sensor as secondary, and then float switches as a third level monitoring technology. The PLC and HMI/SCADA should incorporate mismatch monitoring and alarming.
PLCs and Hardwired Control
While redundant PLCs are available, for smaller systems like the wet well it may be more appropriate to add some basic hardwired controls, such as a high-low level controller, in parallel with a PLC. If the PLC or VFD fails, this type of controller can use bypass contactors to run the pump in a simple on/off manner.
HMI/SCADA
For visualization integrity, designers can consider implementing Ethernet redundant rings and multiple operator stations. It can also make sense to incorporate traditional pushbuttons, switches, lights, and similar devices to provide some bare-bones functionality in the event of an HMI/SCADA failure.
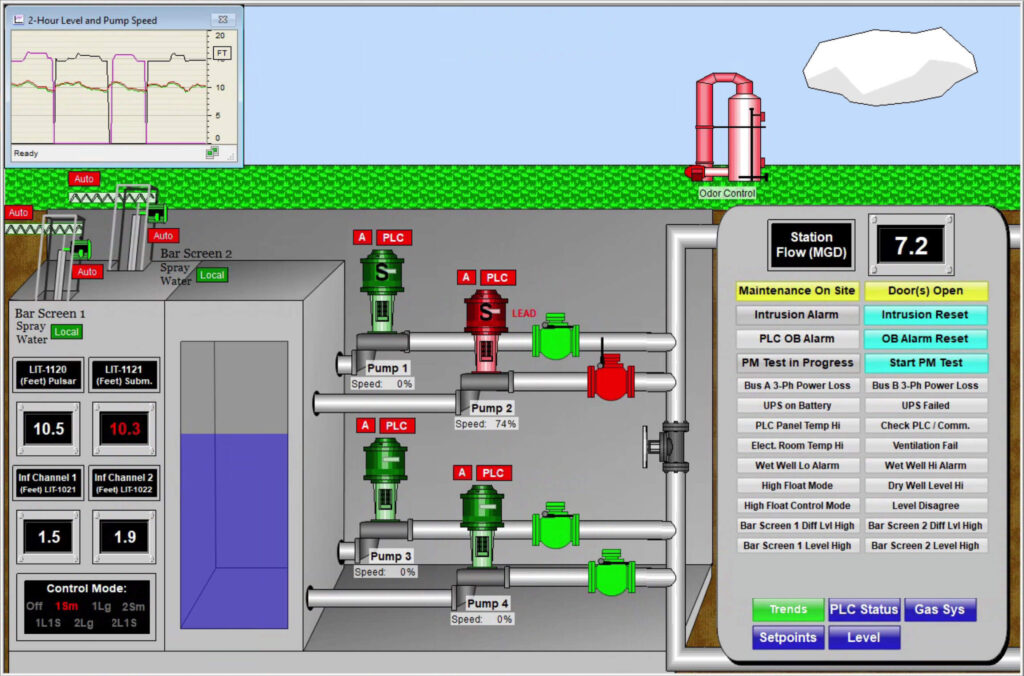
Realistic Redundancy
Applying redundancy to an industrial automation design requires a carefully balanced decision making with regard to price, performance, physical space and other factors. Fortunately, there are many products and design approaches to improve the resiliency of power, measurement, control and visualization systems.
Visit the AutomationDirect website to see all the redundancy products described above, and to find the best fit for your application.