Top tips for supplying clean and regulated air for best pneumatic equipment performance.
Kevin Kakascik, Technical Marketing Engineer at AutomationDirect, wrote an article for the January 2020 issue of Hydraulics & Pneumatics titled The Principles of Pneumatic Air Preparation. Here’s a summary, click on the link above for the full text.
For industrial pneumatics systems, air preparation (often called “air prep”) is a fundamental and often underappreciated necessity. Clean air at the proper pressure is needed for reliable system operation, and for reducing maintenance costs and downtime.
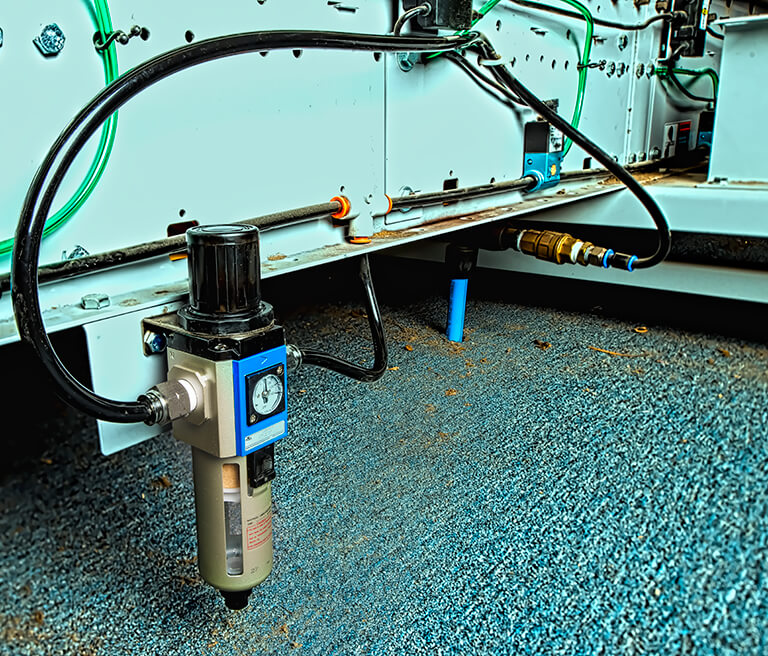
Pressure Basics
Beyond physical connection sizes, pneumatic components are rated for various pressures.
- Operating pressure is the range where the device operates normally
- Proof pressure is how high the pressure can go without damaging the device
- Burst pressure is how high the pressure can go before the device mail fail catastrophically
Disconnects
Designers should always include a means of disconnecting air prep equipment to remove hazardous energy as required by OSHA and ANSI.
- Manual shut-off relief valves isolate downstream equipment, and bleed or “relieve” pressure
- Isolation/lockout valves are like an emergency stop device; they operate similar to manual shut-off valves but are oversized to quickly put downstream equipment in a safe state
- Soft-start valves can dump downstream pressure quickly, but will restore pressure gradually when energized
Filtration
Compressed air can contain tiny but significant contaminants which can wreak havoc on a pneumatic system. Passive centrifugal filters can be used alone or in conjunction with passive coalescing filters to remove dirt and moisture. The moisture must be drained periodically using manual, semi-automatic, or fully automatic provisions. If the air supply contains significant moisture, then an active dryer may be an unavoidable necessity.
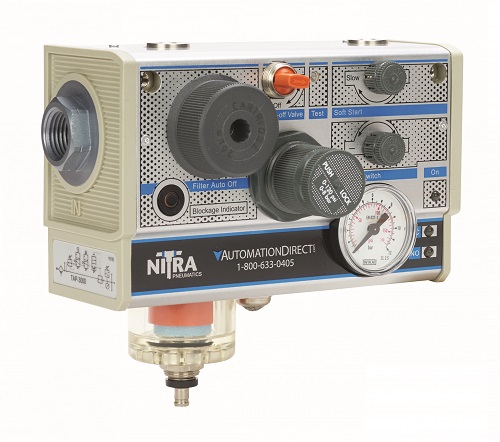
Pressure
Because upstream pressure supplies are generated and maintained at a higher level for distribution, air pressure regulators must be installed to reduce the available pressure to what is needed at the machine or other point of use. Standard and high precision models are available, as are units combining filtration and regulation. Many designers choose total air preparation units, which incorporates a manual shut-off and even a soft-start into the combination package, saving installation space and money.
Lubrication
Most modern pneumatic equipment simply needs clean, dry air. Some older devices and air tools need lubrication, so in these cases lubricators should be installed just upstream of the use point.
An Air Prep System
The normal installation order, from upstream to downstream, of pneumatic air preparation devices is:
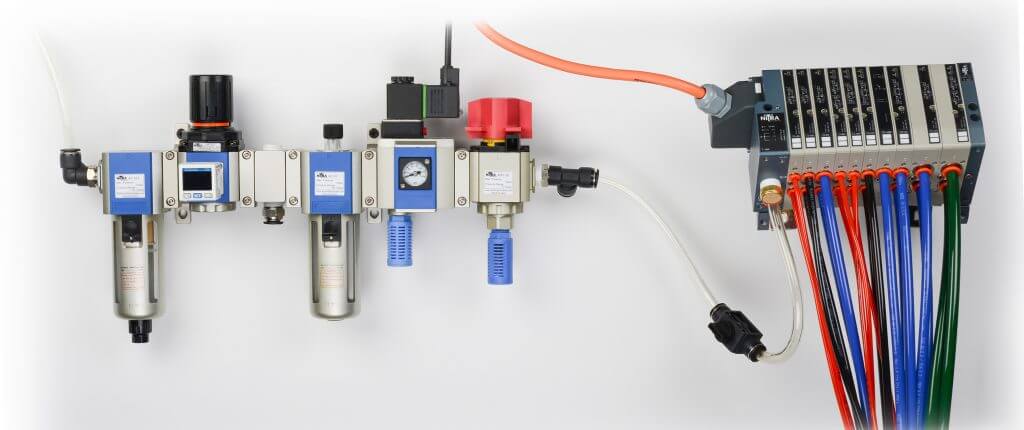
- System isolation valve
- Filter/Regulator
- Lubricator (if needed)
- Device shut-off valve
Users can select the exact right combination of devices needed for their application. Because filtration is typically upstream of regulation, the filter needs to be rated to handle the supply air pressure. Total air preparation units are a useful way to get most of these functions, other than lubrication.
Air preparation design is basic but easy to overlook compared to more active downstream pneumatics elements. Proper air prep will lead to years of reliable pneumatic system performance.