Rodless cylinders are an ideal way to apply pneumatic linear motion for equipment.
Kevin Kakascik, Technical Marketing Engineer at AutomationDirect, wrote an article for the December 2020 issue of Fluid Power World titled Rodless Cylinder Solutions for Compact Pneumatic Linear Motion, discussing how rodless pneumatic cylinders can be a great solution for implementing compact linear motion. Here’s a summary, click on the link above for the full text.
Linear Motion Options
Original equipment manufacturers (OEMs) and systems integrators (SIs) commonly automate machinery needing linear motion control to efficiently and economically meet power, speed, and accuracy requirements.
Electric servo and stepper motors are a high-performance solution, but the design and material costs are high, and for many applications the results are overkill.
Pneumatic cylinders can be effective and a relative bargain if the form factor is suitable. However, traditional cylinders are long tubes with an internal piston connected to a rod that extends and retracts as air pressure is introduced or exhausted. These devices are best for complete-stroke applications, and they usually require installation space at the end of the driven equipment, so they tend to consume a lot of “footprint”.
An alternate pneumatic option is a rodless cylinder, which works similarly to a traditional double-acting rodded cylinder. Rodless cylinders also have an internal piston, but instead of connecting to a rod at the end, they connect with an external carriage that moves alongside the cylinder body, allowing them to be packaged into tighter spaces.
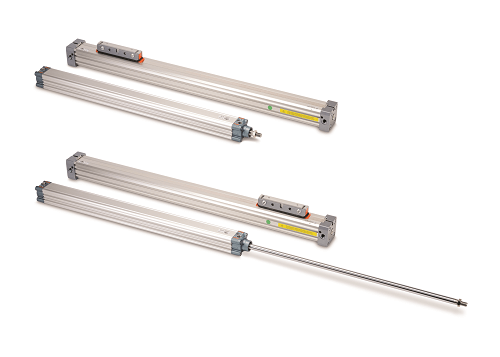
Rodless Solutions
Rodless cylinders can be a great solution for sticky situations, such as for a glue station where the glue head needs to travel across a flat sheet of cardboard, but the equipment must be installed into a tight space. A pneumatic cylinder is ideal for driving this type of motion, but traditional rodded versions would overhang away from the machine quite a bit, often creating installation issues, and perhaps safety concerns. A rodless version will compactly fit within the machine footprint, reducing complexity and cost because it acts as the glue head support with no other mechanism required.
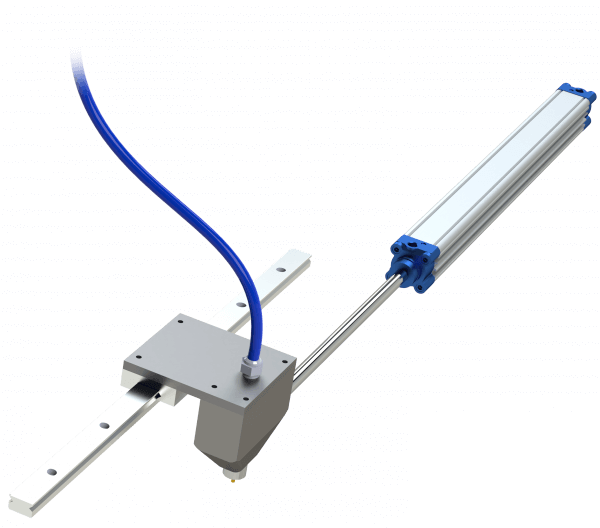
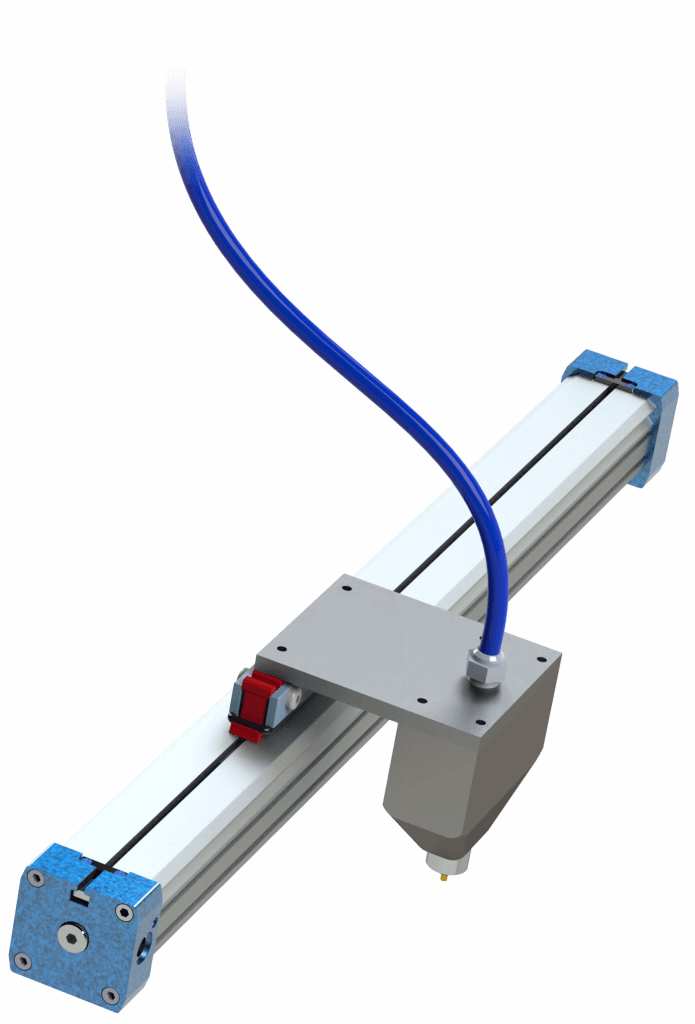
For the same reasons, a rodless cylinder can be the best solution for vertical applications like a punch station. In this case, reducing the overhead height of the equipment ensured code compliance by keeping the proper clearance away from overhead sprinklers.
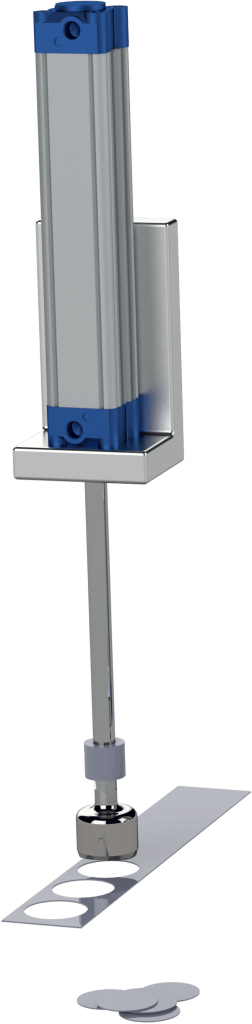
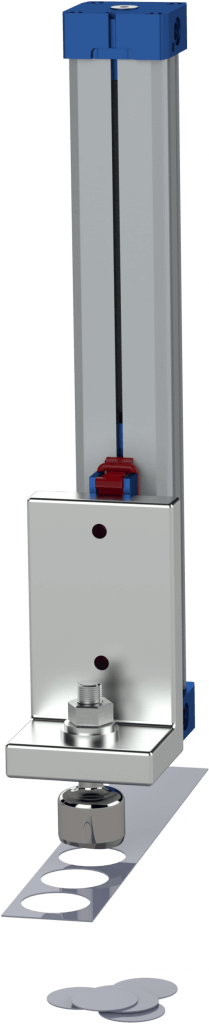
Solving Linear Motion Problems with Rodless Cylinders
Rodless cylinders are more expensive than their rodded counterparts, but they are far less costly than electric motor-driven options.
However, where space is at a premium for linear motion, especially for long stroke lengths, a rodless cylinder can often be used in place of a traditional rodded cylinder, especially if the mechanism will be attached to a carriage.
AutomationDirect offers many rodless cylinder options and can help designers choose the best solutions for their linear motion applications.