Sensible Automation Solutions updated its customer to an AutomationDirect BRX Do-more PLC to add needed capabilities and data reporting to an existing wastewater treatment system.
James Catlett, president of Sensible Automation Solutions, wrote an article for the November 2018 issue of Control magazine titled SCADA Upgrade Provides Quick Compliance.
A local municipality wanted confirmation, and the data to prove it, that the wastewater released to the sewer system by a large agricultural component manufacturer was within county standards, and they wanted it immediately. Catlett says what made this request difficult was that the current wastewater treatment system in the plant used only manual data logging, and had other shortcomings.
What made it worse was that the system’s process measurement instrumentation was uncalibrated and unvalidated, resulting in unreliable chemical dosing.
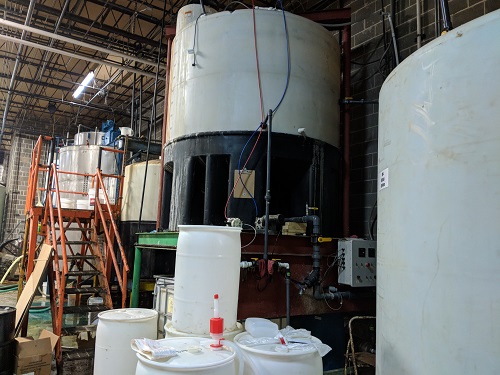
Acid and caustic tanks hold the acid and caustic needed to balance the PH of the wastewater produced from a large agriculture components metal coating process.
Sensible Automation Solutions was brought in to quickly upgrade the wastewater treatment system. Although the original system operated well with an AutomationDirect Click PLC and C-more HMI, Catlett says it couldn’t be used to meet the advanced requirements now demanded by the municipality.
It was necessary to add automatic data logging in place of the manual data logging. The agricultural component manufacturer also requested daily reports on the wastewater system process data, with the ability to email this information to its managers. None of this functionality was available with the Click PLC, so we chose the AutomationDirect BRX PLC to replace the existing controller and meet requirements.
Getting Control of an Existing Facility
The control system upgrade was performed on the existing wastewater treatment system. The system treats wastewater from the metal coating side of the plant, and it supports the powder coating line, which uses a variety of chemicals.
Catlett says the BRX PLC was a cost effective and capable choice for this system, made easier because technicians at the facility had prior experience with AutomationDirect.
Sensible Automation Solutions has used a lot of PLCs in the past, but the BRX brings new capabilities for its form factor and cost. It’s a small, brick-type PLC with analog inputs and outputs, configurable high-speed inputs, and high-speed outputs—filling the needs of many different processes. The PLC’s Do-more programming software is powerful yet easy to use, adding to the appeal of the platform.
Another reason the BRX was chosen was because it fit in the panel space originally occupied by the small Click PLC.
We simply unwired the existing Click controller and installed the BRX, along with ZIPLink connector modules and cables, and re-attached the existing power and field wiring. Everything fit with minimal required changes and wiring additions.
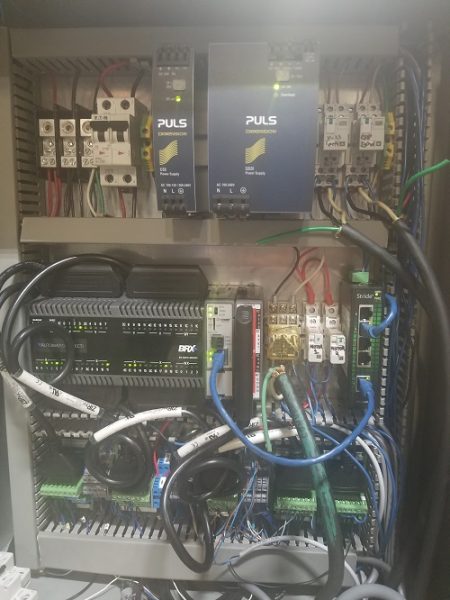
This new AutomationDirect BRX PLC replaced the existing Click controller with minimal required changes or wiring additions.
Process Details
The system logs pH data throughout the day including how much acid or base is being added and when, and how much water has been discharged. The BRX PLC controls two 15-GPM diaphragm pumps used to feed the acidic or base solution to the pit based on the monitored pH levels.
The flowmeter added to the system had high speed outputs proportional to flow that could be read by the BRX PLC. Since this flow data and other data was logged and sent to the municipality, it needed to be accurately date-stamped, and the PLC provided this capability with its built-in clock.
The program to control the system was written from scratch for use in the new BRX PLC using the Do-more Designer Software. The facility provided a sequence of operations defining how it wanted the system to work. Ladder logic was then used to create a program to satisfy the requirements of the provided process sequence.
A new HMI was programmed and linked to the new PLC to provide the required functionality.
The new control system includes an AutomationDirect C-more EA9 Series 15-inch touch panel HMI. A new graphical interface program was created from scratch to take advantage of the C-more’s capabilities. Screens were added for data trending, allowing viewing of historical data for the last few hours. Screens were also added to view logged data from previous days. New operational screens were provided to view the level of the pit, dosing activity and general process status.
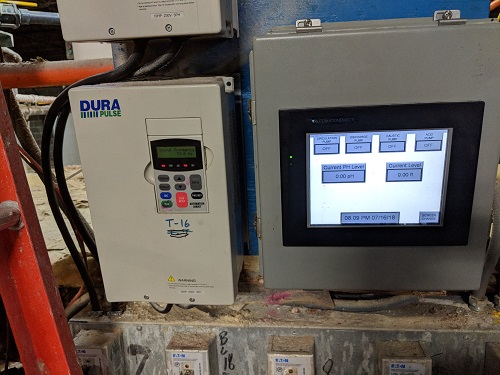
An AutomationDirect C-more EA9 Series 15-inch touch panel HMI was added to the new control system to provide status, data trending, historical data, reporting and other functions.
Installation Aids
It was tricky to install the equipment—and time sensitive. Catlett says the facility runs 24/7, so only six hours of shutdown time were available to remove the old controller, install the new one, power up, debug and test the system.
The automation system creates reports and sends them via emails. For example, every day at 12:01 am, or any configured time, the C-more panel is setup to transfer the data via email to company managers. The automation system also sends out other specialized reports such as how much of acid and base solution was used throughout the day. Catlett says the job was done quickly.
The biggest challenge was doing the work quickly to satisfy the local authorities. To meet this requirement, Sensible Automation Solutions installed the new automation system within 10 days after the first call from the agricultural component manufacturer.
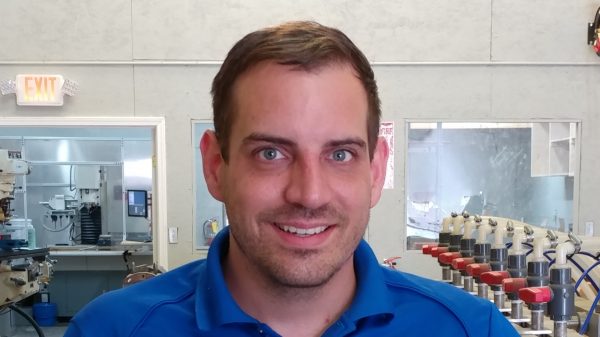
James Catlett, president of Sensible Automation Solutions
To read more articles related to wastewater management, click here.
Originally Published: December 2018