Because AC motors are essential workhorses for industry, designers need to understand their applications to make detailed selections, such as single-phase or three-phase styles.
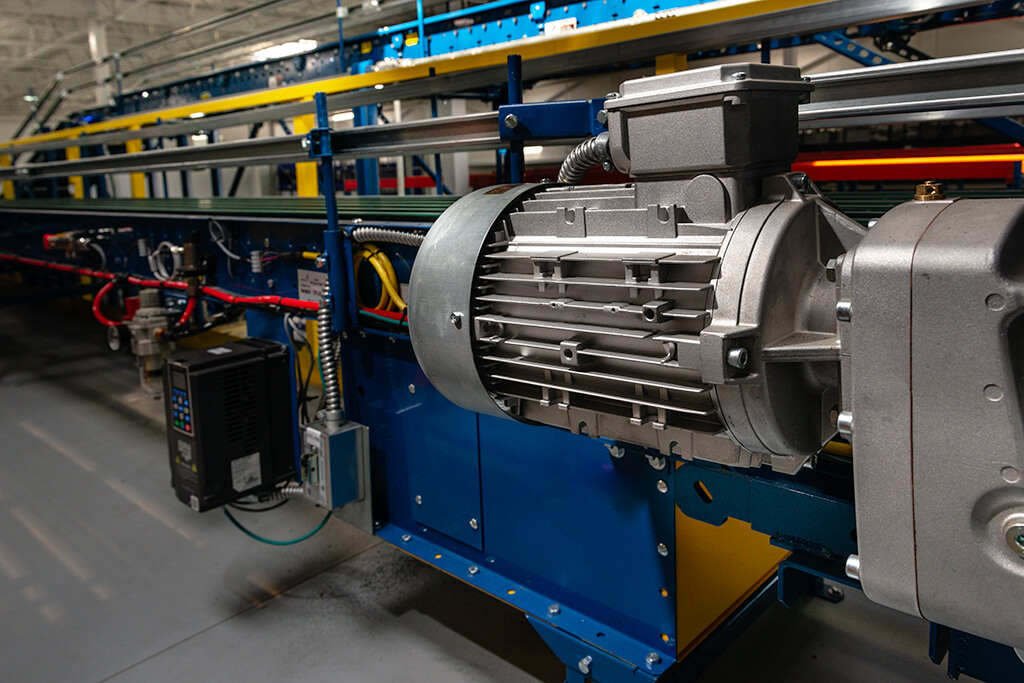
Electric motors are a fundamental force for creating powered motion in any type of equipment. Initially developed in the 1800’s and refined significantly over the years, electric motors are now available in several styles. The earliest types of motors were direct current (DC) and alternating current (AC) induction, and these have been the workhorses of modern machinery ever since they were first applied during the Industrial Revolution.
Although DC motors have traditionally offered some advantages for lower-cost speed control and high starting torque, AC motors are generally simpler (as explained below), economical, and provide higher efficiency. Because AC motors are so commonly used for commercial and industrial applications, it is important to understand the difference between single-phase (1-Ph) and three-phase (3-Ph) AC induction motors.
Electric Motor Basics
Any electric motor converts electrical energy into mechanical energy through the interaction of magnetic fields. An AC motor has a fixed winding called a stator. When AC current is supplied to the stator, it generates a rotating magnetic field, which acts upon the rotor—a rotating portion inside of the motor—which reacts to this field and creates the spinning action.
Unlike most DC motors, AC motors do not require any extra electronics, or complexity like inefficient brushes. AC motors can be used directly with line voltage, and three-phase motors can be controlled with a variable frequency drive (VFD) to provide speed control and other features (Figure 1).
Throughout the world, AC power generation and distribution systems are the most common form of electrical utilities, making AC motors convenient to use. While there are many electrical service options throughout the world, in the United States the three most common are:
- 120V/240V: 1-Ph 3-wire split-phase center-tapped, often for residential
- 120V/208V: 3-Ph 4-wire wye, often for commercial
- 277V/480V: 3-Ph 4-wire wye, often for industrial
Higher voltages permit greater energy transfer at lower currents, compared to lower voltages, and therefore can use smaller conductors. In a home application, the air handler fan motor is usually 120V 1-Ph, while the more power-hungry air conditioning compressor would be 240V 1-Ph. For commercial applications, it is common to see 208V 3-Ph for HVAC motor loads. At an industrial site with even larger motor loads, 480V 3-Ph is the most common supply voltage.
Single-Phase Specifics
For a single-phase motor, the stator winding consists of a series of coils arranged around the rotor. When an AC current is applied to the stator, it generates a single north/south magnetic field, rotating at the line frequency. At full speed, the rotor will spin in accordance with these fields.
However, without other provisions, when a single-phase motor is energized to start from a completely stopped condition, the motor would remain stalled, or if it does run it might do so forward or backward depending on its initial position. To overcome this problem, AC motors commonly include a secondary starting coil wired in series with a capacitor. Upon startup, this circuit causes a magnetic field phase shift, which starts the rotor turning in a predictable direction. Once the rotor is spinning sufficiently fast, a centrifugal switch opens to disconnect this starting circuit. The starting coil is designed to define the desired rotation direction.
Three-Phase Specifics
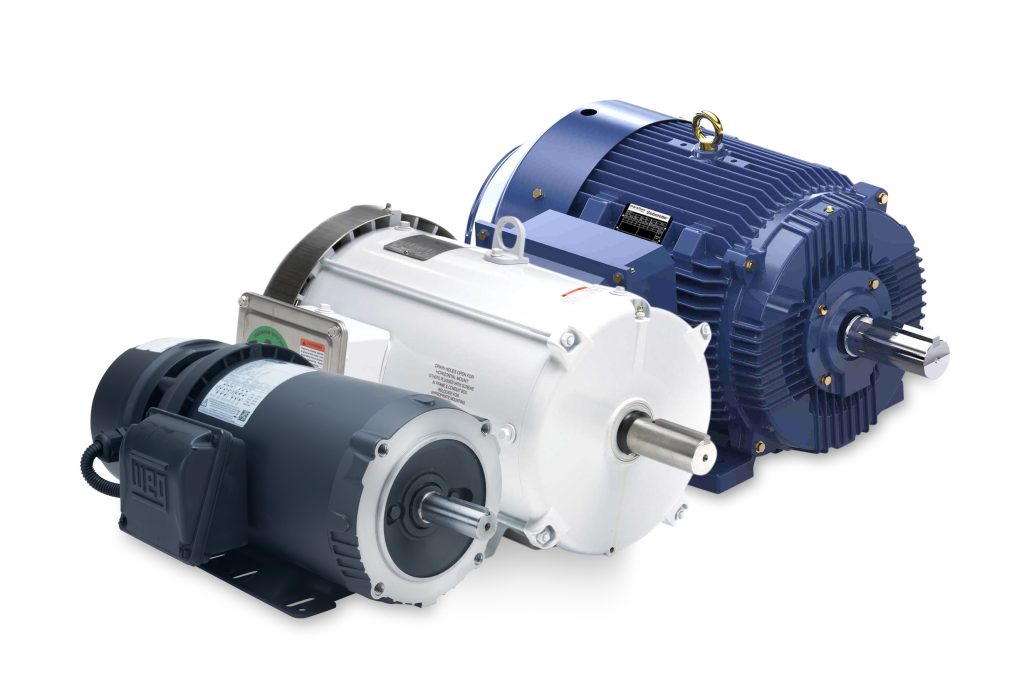
A three-phase motor also has coils, but the three phases are arranged every 120° around the rotor. Because the utility supplies each of the three electrical phases in a rotating sequence, the direction of sequence will positively define the rotor direction, and no starting coil is needed. If a motor is initially connected and is found to spin in the wrong direction, the installer simply reverses two power leads to switch the direction.
An additional benefit of three-phase motors, compared with single-phase motors, is that each of the three three-phase conductors will carry less current than the two single-phase conductors for a given horsepower.
Choosing Single-Phase or Three-Phase Motors
The choice of single-phase or three-phase motors is largely based on what electrical supply is available at the site where they will be used (Figure 2). That being said, almost all residential and many smaller commercial or shop applications, including appliances and light machinery, will use single-phase motors. They will commonly be 120V for smaller loads, and 240V or 277V 1-Ph for larger loads.
There are some single-phase motors of 5HP or larger, but designers will lean toward three-phase motors for most applications of that size. For these larger industrial applications, three-phase motors are usually the best fit. Of course, when specifying a motor, there are other important considerations, such as:
- Horsepower (HP) and speed
- Efficiency rating
- VFD-rated windings (for three-phase motors) if the motor will be used in this service
- Mounting provisions
- NEMA frame size
- Multi-voltage (configurable to run at more than one voltage; simplifies stocking of spares)
- Environmental enclosure rating
The AutomationDirect website offers a broad selection of AC induction motors. There are also DC motors and accessories, as well as a complete range of motor controls, including disconnects, starters/contactors, VFDs, and DC drives. The site also includes plenty of information resources, specifications, documents/drawings, and videos—and support staff are ready by phone and email to help you find the right motor products for your applications.