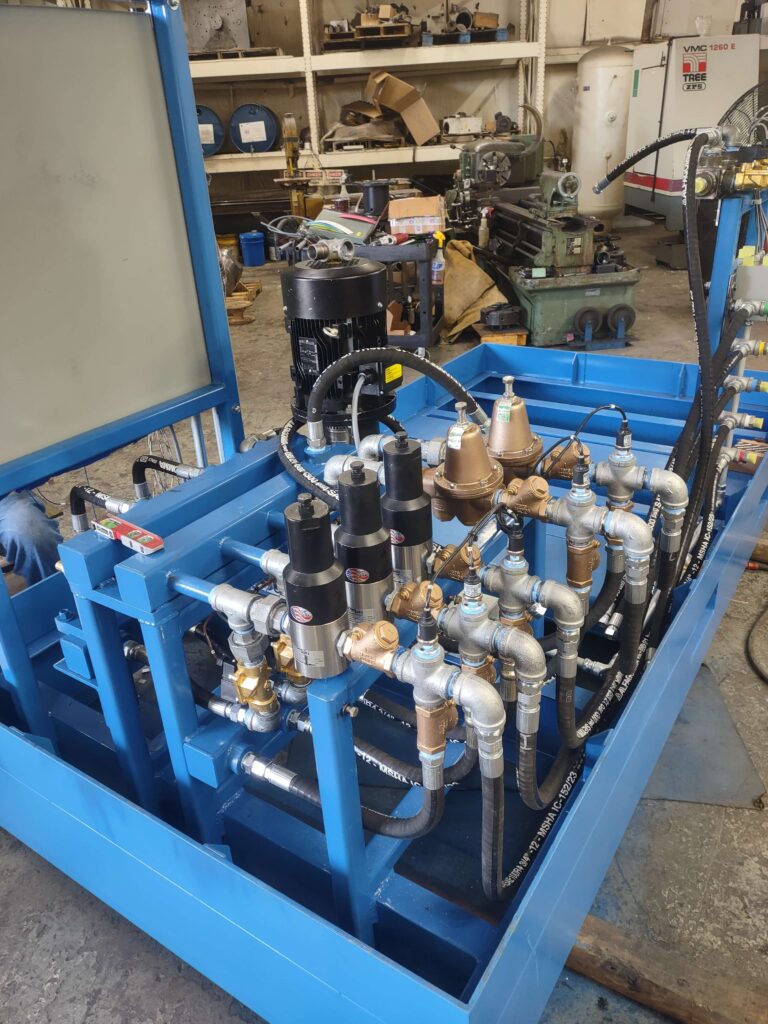
By partnering with a local systems integrator and using AutomationDirect products, this machine shop enhanced its capabilities, allowing it to deliver the services required by its customers.
Throughout the country, networks of small businesses—including machine shops and systems integrators (SIs)—innovate and integrate to deliver successful projects. One example is a collaboration between Stephens Machine and Par Electric & Engineering in Kokomo, IN. In an Automation.com Jan 2024 article titled Case Study: Machine Shop Expands with Automation, Par founder Pete Baker explains how the two companies teamed up to deliver a high-performance pressure testing solution.
Working Under Pressure
A metal casting manufacturer required automated equipment able to detect any casting flaws, each of which could lead to failure of the final product. While their chosen machine shop could build the hardware, piping, and valves to create the hydraulic equipment needed to perform the required pressure testing sequences, they did not have the automation capabilities in-house. To rectify this issue, they collaborated with local SI Par Electric to take the lead on electrical design and programming.
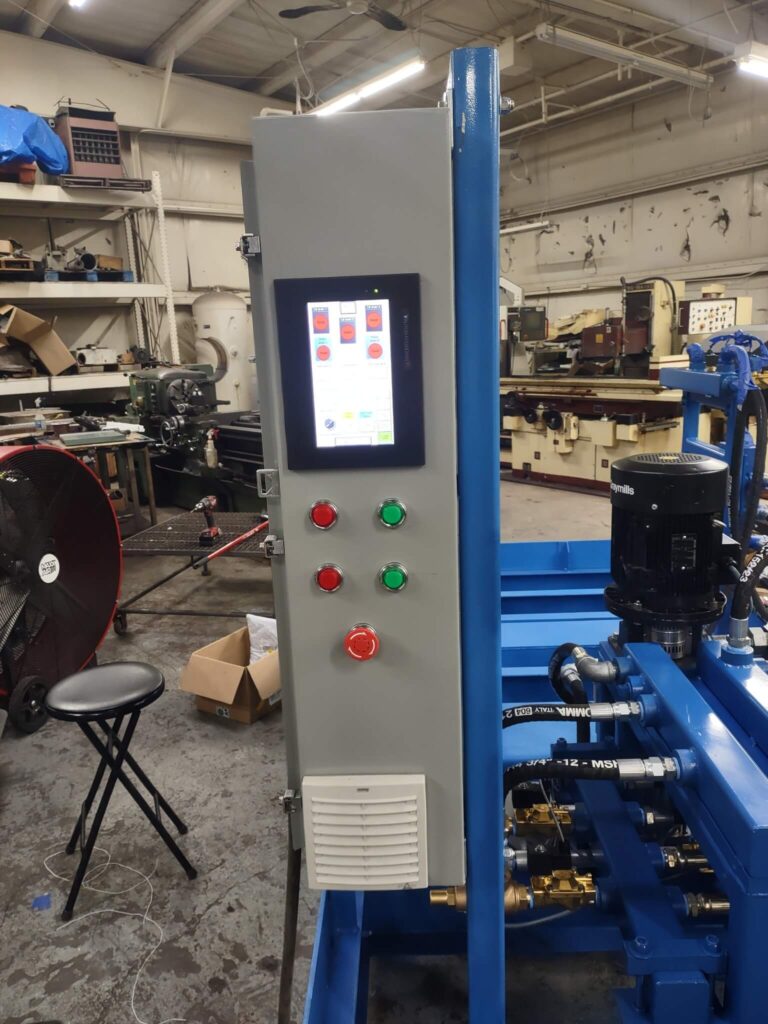
A control panel would be needed to operate a hydraulic pump motor, sequence 13 directional control valves through a manifold system, and introduce pressurized fluid to the casting over three phases of increasing pressure. Once a given pressure was established, any pressure bleed-down in the following minutes would indicate a problem.
Creating a Tough Testing Solution
Based on numerous prior positive experiences with AutomationDirect products, Par Electric designed and built a PLC/HMI control panel based on a Productivity2000 PLC and a C-more HMI, along with circuit breakers, a control power transformer, a motor starter, interposing control relays, safety relay, and more. The SI appreciated the quick shipping and streamlined procurement process.
The PLC interacts with about 50 discrete and analog I/O points. Due to the sequential nature of the testing functions, the team used classic drum sequencer instructions to operate the valves. Math computations and timing functions were used to evaluate if pressure decay during a testing sequence was within acceptable thresholds.
Because of the compact equipment arrangement, this application used the HMI in portrait orientation—and also incorporated industrial 30mm pushbuttons—on the side of the control panel. This provided the best visibility for operators, allowing the equipment operational step, pass/fail results, and threshold settings to be easily and quickly accessed.
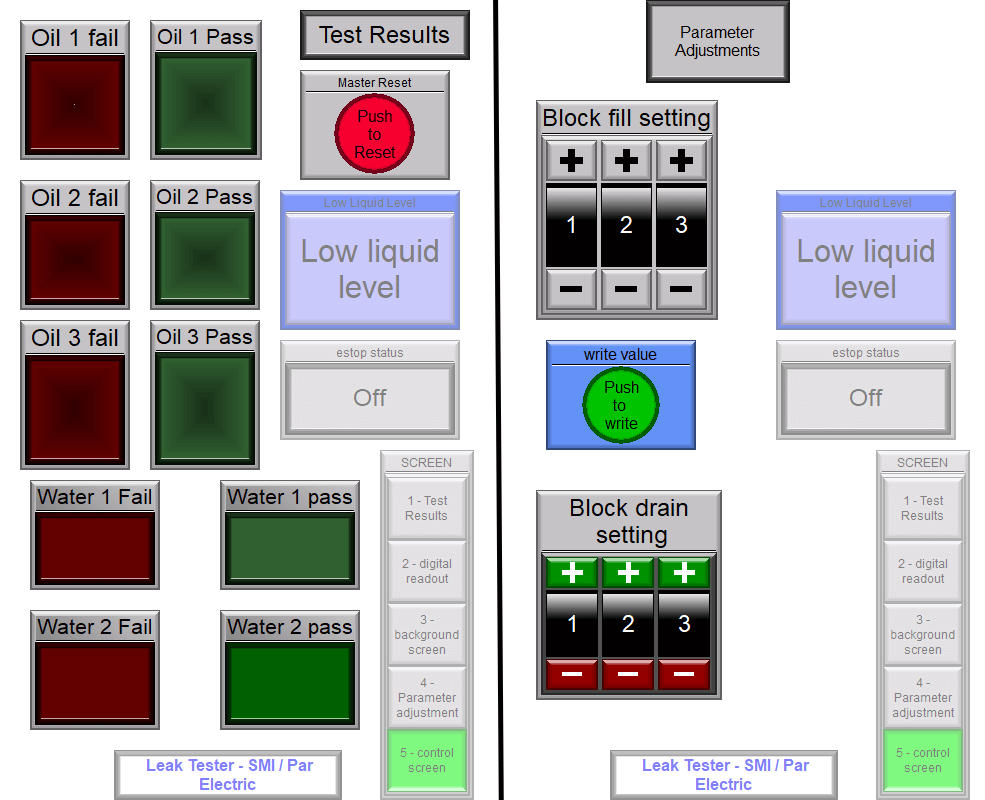
AutomationDirect development software is available free of charge, and it includes simulation tools that empower users to easily test and debug the code. Although the current system does not take advantage of remote connectivity or cloud access, these capabilities are readily available for future incorporation.
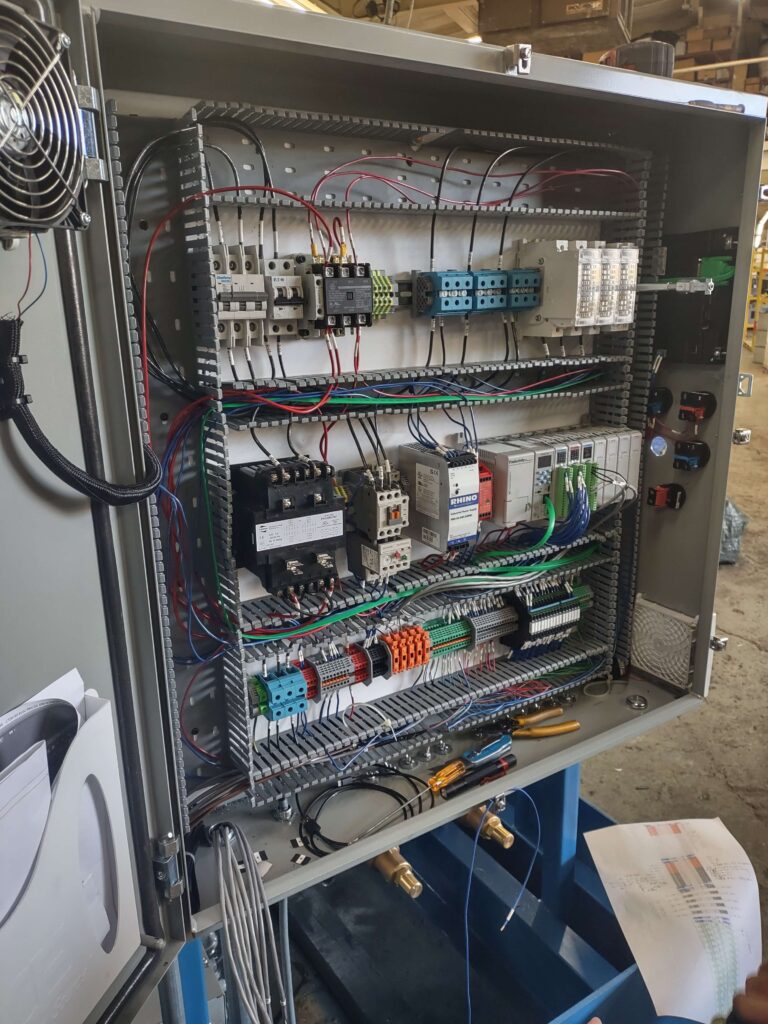
There are many routes to success and partnerships are often a cornerstone for growth, especially for small businesses. In this case, working with a SI enabled a machine shop to enhance their product offering and better support their customer. Adding automation to their machined and assembled test stand was a great project for collaboration and all parties involved were thrilled with the results.
Visit the AutomationDirect.com website today to find a variety of solutions that make it possible for your company to expand its capabilities.
All figures courtesy of Par Electric & Engineering
Originally Published: January 2024