Using the AutomationDirect Do-more BRX PLC, an extrusion company progressively upgraded and simplified their legacy manufacturing lines, greatly improving performance, while minimizing scrap.
The situation is common at many manufacturing sites: production equipment is old, degrading, and mismatched, leading to operational and maintenance inefficiencies and nightmares.
In an April 2022 Automation.com article bylined by Gary Lucas, titled Controls Upgrade Makes the Cut, he describes how an extrusion line was upgraded with a modern PLC and HMI to overcome these challenges and create a highly efficient production line.
Extrusion Production
Extruders compound material, such as plastic, force it through a die to create a continuous product with a desired profile, then cool/pull/cut the material as needed to end up with a final product. Sometimes there are many different products produced, requiring changeovers. At the subject site, there were four production lines of this type, with lots of manual user interaction needed. This created operational problems, along with high reject rates and scrap. Temperature control and motor/motion control improvements were needed, along with other upgrades.
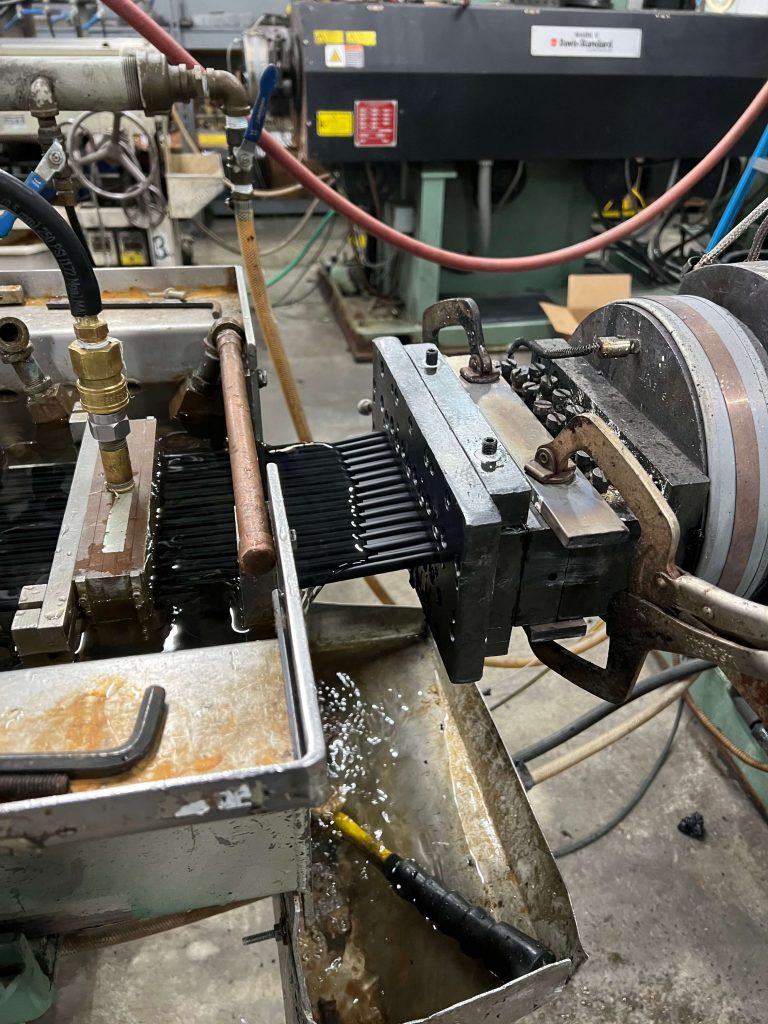
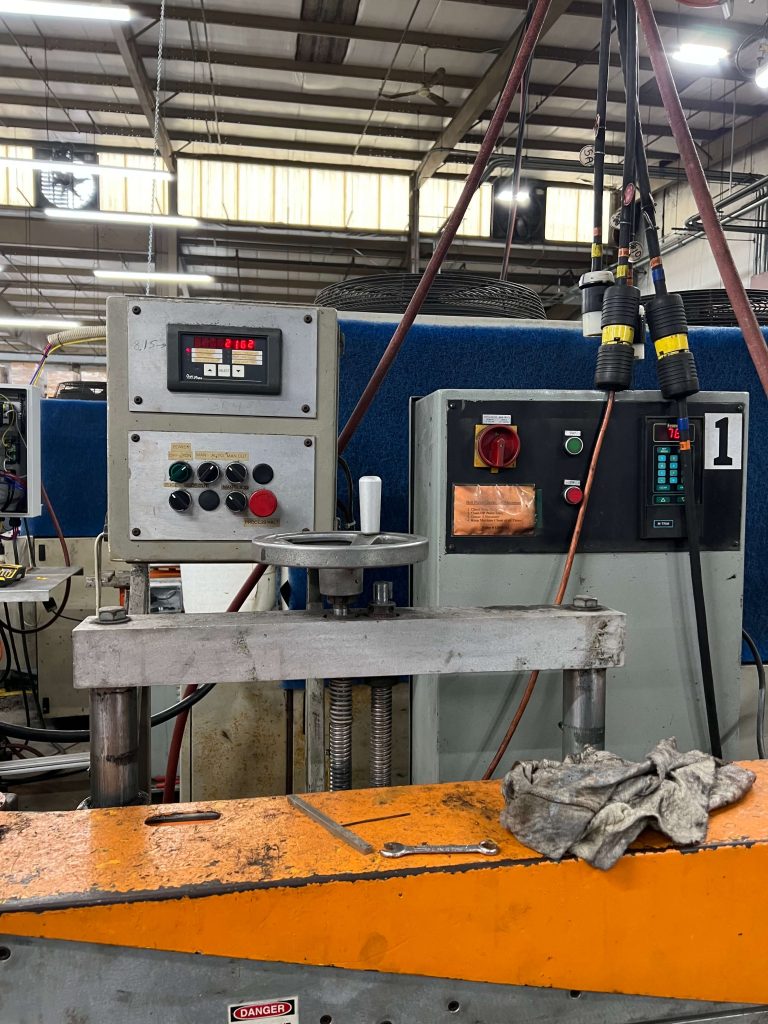
Modernization Masters the Mess
Each of the extrusion line functions was handled by individual controls. The team knew the automation of each step could be improved with the right PLC/HMI platform, which could also be used to make upstream/downstream coordination seamless. The first step was to design a control panel around the AutomationDirect Do-more BRX PLC, C-more HMI, Rhino power supply, StrideLinx router, Koyo encoder, and other components.
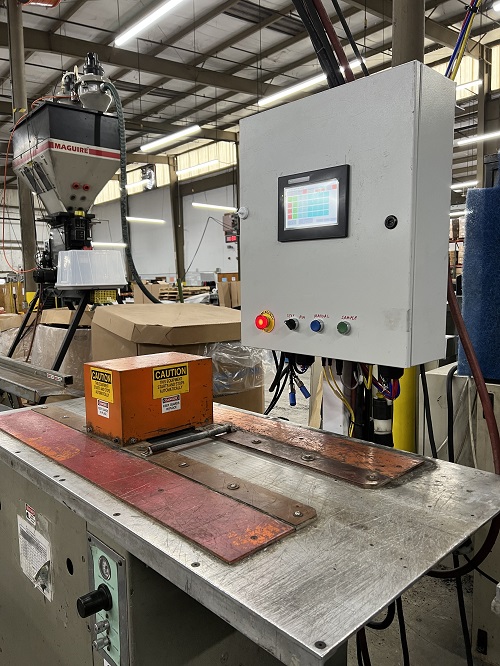
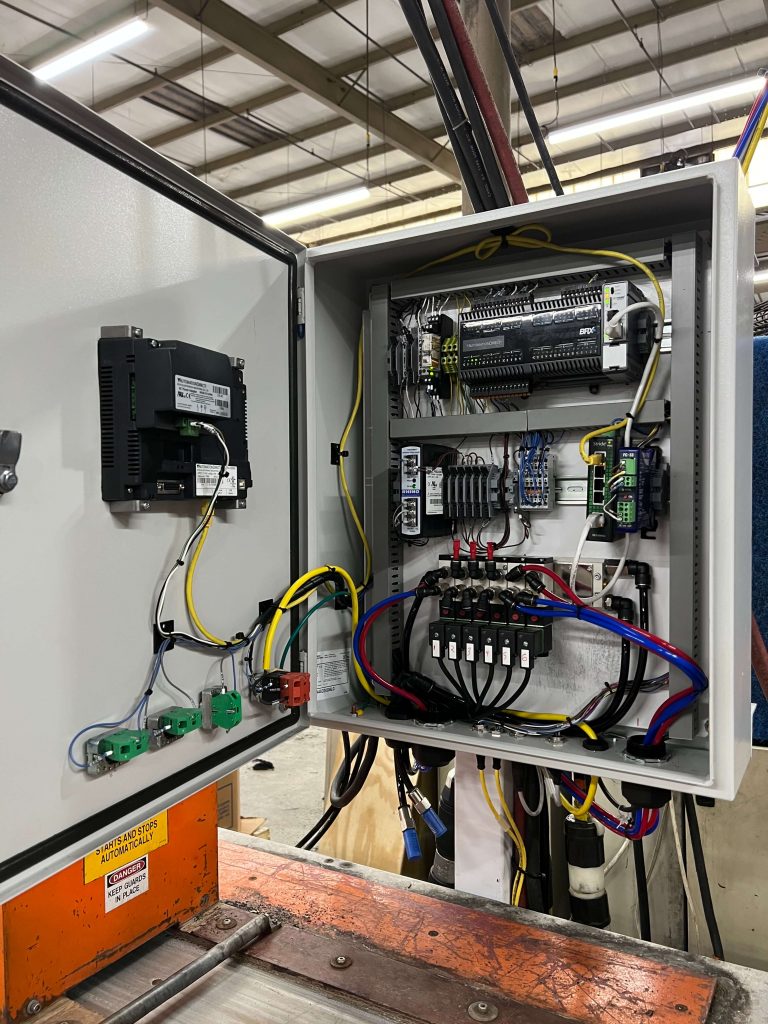
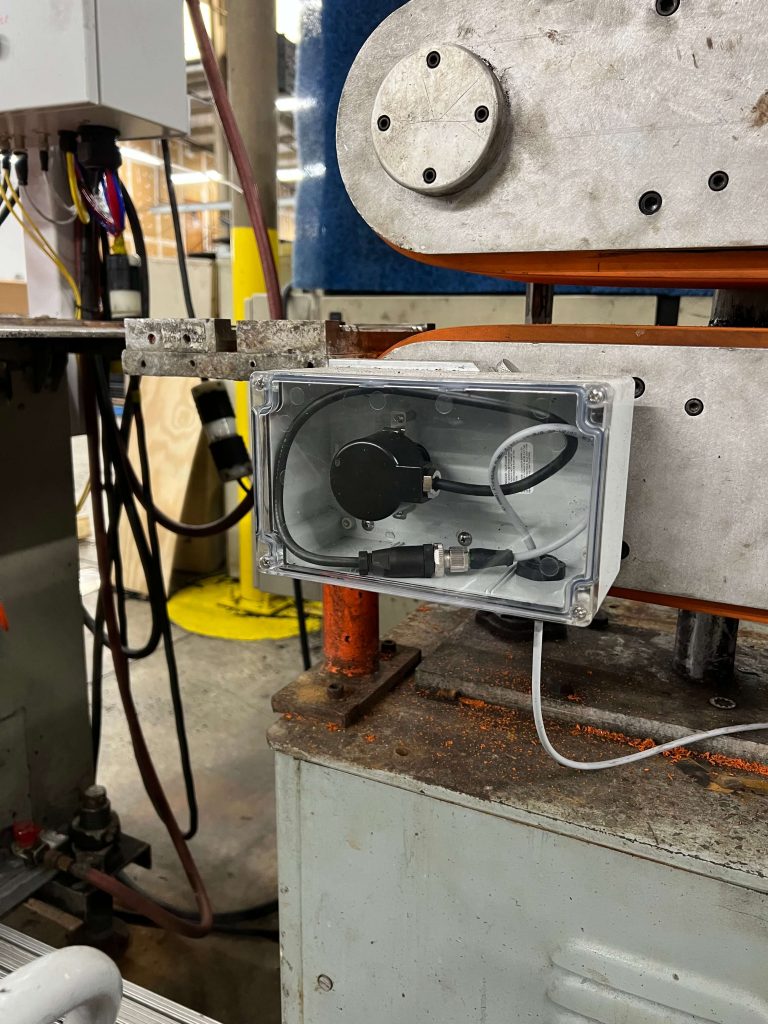
The first upgrade used a new encoder and PLC-based PID control to provide accurate speed control and display, overcoming deficiencies with the old system. The autotune process took less than a minute. Subsequent incremental upgrades were based on the same encoder signal, delivering properly coordinated flying cutoff and other slicing operations. The HMI/PLC used a recipe system for easy product changeovers, along with simple fine-tuning when needed. Each upgrade was staged to minimize impacts to production.
Better Quality and Ease-of-Use
Operators appreciated the practical and clear interface, and the fact that they did not need to scramble around the machines and make mechanical and sensor adjustments for project changeovers or to keep things running smoothly. New functionality can be triggered via the HMI to produce a short sample between product cuts, so there is no unnecessary waste. Maintenance personnel can also take advantage of password protected diagnostics and troubleshooting displays.
Automation Upgrade Delivers Benefits
Many end users have one or more systems that need upgrades to remain serviceable. Large all-or-nothing rip-and-replace retrofits are risky to pull off and involve lots of downtime. For this client, we were able to use AutomationDirect products almost exclusively to create a control system retrofit platform that was flexible enough to be incrementally and progressively deployed.
As an added benefit, once the system was proven on one production line, the team was ready to rapidly replicate it to the other three lines.
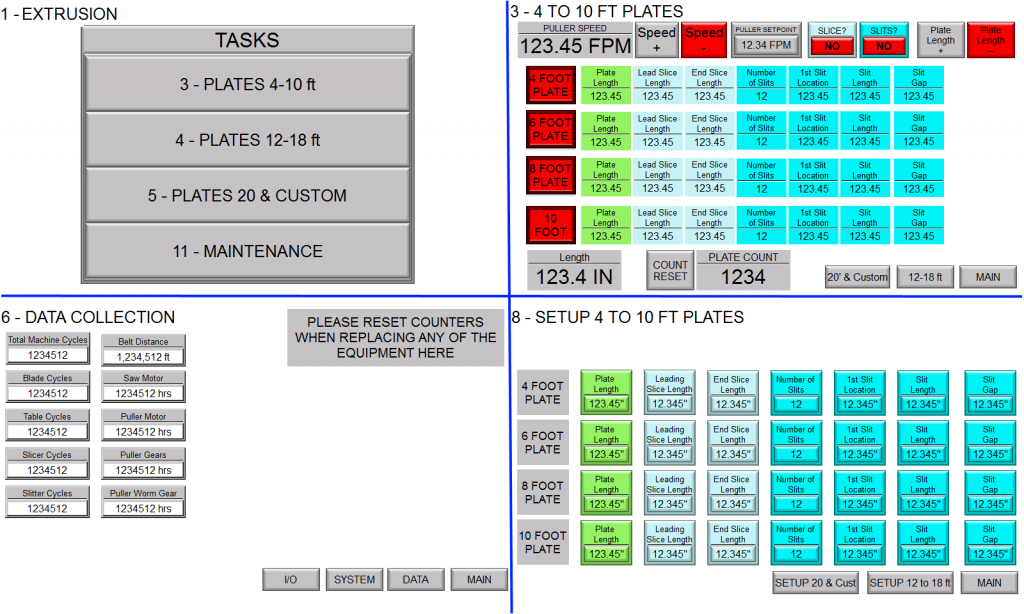
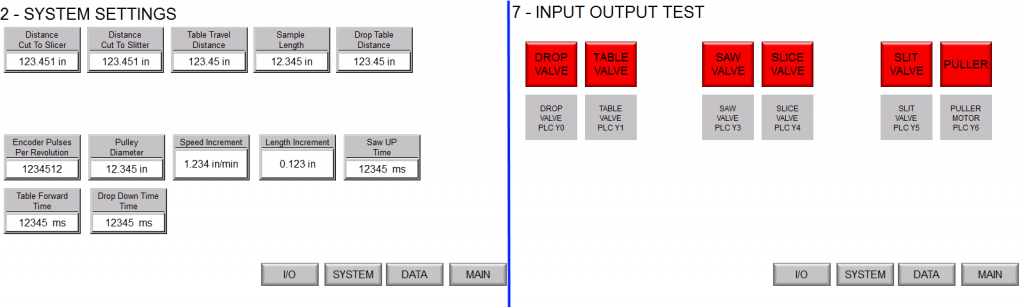
All figures courtesy of Gary Lucas