Broadcasting is a high tech industry and much of it is cutting edge, such as Ethernet-based audio over IP. Our industry employs the latest technology in many areas, such as the use of coding algorithms for bit rate reduction and remote broadcasting. But when it comes to controlling the radio signals sent out by the transmitter, most stations are still doing things the same way they have for a long time.
Controlling the broadcast hardware connected to the antenna—and the related transmission power, source and facilities—is still low tech. Typically, the broadcast engineer gets in his or her car and drives to the unattended transmitter, translator or repeater site (Figure 1) to flip switches and make other manual adjustments.
In radio and TV broadcasting, it’s easy to get distracted by the acoustics, microphones and audio processing. But it’s also important to focus on the transmission system because this is where all of the hard work in the studio is disseminated to listeners.
I love the broadcast industry and have been working in it for 46 years. I’ve been using programmable logic controllers (PLCs) to automate broadcasting functions that have been traditionally very manual, or custom and semi-automatic at best. This article shows how I automated the switching and backup functions of an antenna and transmitter system to improve operations, cut costs and improve reliability. It also provides a path for others in the industry to automate their broadcast and other facilities with PLCs, just as I’ve done.
Serving Southern California
iHeartMedia oversees 10 radio stations in a geographical area the size of South Carolina. The LA metro area is enormous in terms of population, which presents opportunities and challenges. In addition to radio stations, iHeartMedia owns outdoor advertising and also has a large online radio presence in the form of the iHeartRADIO app. The station broadcasts in digital, HD radio and old-fashioned FM.
The iHeartMedia website (www.iheatmedia.com) claims over a quarter of a billion monthly listeners in the U.S. and has the largest reach of any radio or television outlet in America. It owns and operates 858 broadcast radio stations serving more than 150 markets throughout the U.S., so there are many transmitter sites controlling AM and FM radio signal transmission.
In the old days, controlling the audio, antenna and transmitter was strictly a manual process. In more recent times, broadcast-specific remote control systems have been deployed to provide rudimentary control via dialup modem. With these systems, alarms can be setup to notify personnel by phone or email if there is an issue. The systems can also have macros programmed to handle automatic functions. The problem is that the cost, reliability and simplicity of these systems don’t come close to what the PLC can deliver.
Interfacing and Control with PLCs
The use of PLCs in broadcasting to control transmitter functions is a topic broadcast engineers don’t know much about. Discussing a common piece of broadcast equipment, such as audio mixers and audio distribution amplifiers, is easily understood in the broadcast industry. The use of PLCs to perform broadcast functions is not. Ladder logic and tag databases are not well understood, so the learning curve is steep.
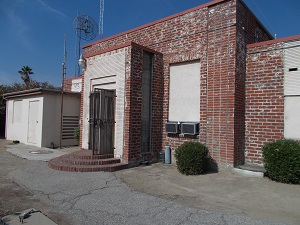
Many transmitter sites, such as this KLAC radio station facility in Los Angeles, are remote and unattended.
Although many broadcast engineers don’t realize it, the hardware commonly used in industrial automation works well for control and monitoring of transmission facilities. 50,000 Watt transmitter sites consume about 150 kW of power and contain air conditioning, power distribution and backup power systems.
Over the years, broadcast engineers have upgraded manual monitoring of transmission facilities by applying custom electrical cabinets filled with relays, timers, diodes and capacitors. Some are even taking a Raspberry Pi and interfacing it to a motor or blower fan using contactors and relays, which is not the simplest, most cost-effective, or the most robust design. By contrast, a PLC is designed to reliably control contactors, relays and other components in an industrial setting.
Many broadcast engineers spend a lot of time developing interfaces among different components and items of audio equipment. They take a transmitter manufactured by one company, an audio processor made by someone else, and a remote control system by yet another manufacturer and connect them together along with air conditioners, electrical distribution panels and exhaust blowers. They then figure out a way to integrate it all into a system, but the control hardware they use is often not suited to the task.
Automating Broadcast Functions
Automatic failure switchover and remote access are sorely needed in broadcast because many of the remote transmitter sites aren’t readily accessible, particularly during periods of inclement weather. The discrete manufacturing and process control industries have been automating with PLCs for years to provide remote access and other advanced functionality, and we’re now adapting this technology to broadcasting.
An application that highlights the use of PLCs in the broadcast industry is at our Dodgers Flagship station in Los Angeles, KLAC AM 570. In this application, we’re using the AutomationDirect Productivity2000 controller (Figure 2) as an antenna/transmitter controller, and we chose this PLC for a number of reasons.
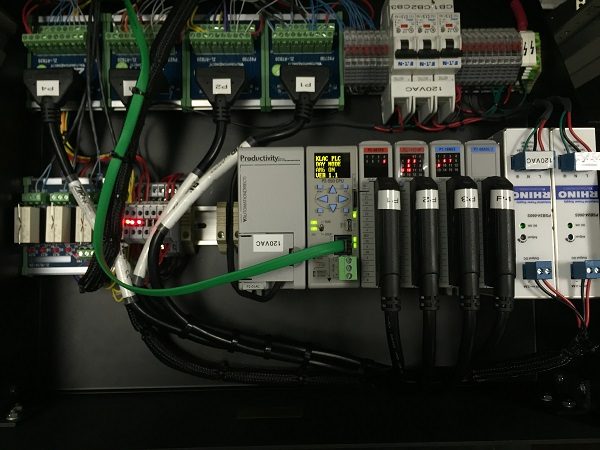
An AutomationDirect Productivity2000 PLC was used to automate transmitter pattern and backup switching at a remote facility.
We’ve used the AutomationDirect CLICK controller in the past for transmitter control and it worked well. However, for the KLAC antenna/transmitter controller, we wanted to add more features. This included email notifications anytime the system did a transmitter pattern change or an error occurred, which is a built-in function of the Productivity2000 PLC. It also has PID built-in, which will be needed for building environmental control when added in a future project.
KLAC is a directional, amplitude-modulated (AM) radio station. In the daytime, it operates using a single tower (antenna) in non-directional mode, which is common in broadcasting at AM stations. At night, it uses two towers to produce a more directional signal to avoid interference with other stations on the same frequency, which is needed because AM signals travel farther at night. This pattern change is required and defined in the station’s license from the FCC.
The PLC automates the switching between daytime and nighttime patterns. Using the real-time clock in the controller, we built a table to control the switching time in compliance with FCC regulations. The PLC performs the automated pattern change and sends an email to confirm.
Reliable Broadcasting
The Productivity2000 PLC and an AutomationDirect C-more touch panel display are the main components of the automation system also used to control and monitor the status of the station’s main and backup transmitters. When we are broadcasting a Dodgers game, the station absolutely has to be on the air, and the reliability of the PLC ensures a continuous transmission signal.
The PLC monitors the status of the main transmitter and will try to restart it if it fails. If unsuccessful, it automatically switches to the backup transmitter. If the backup fails, it switches to a third level transmitter and lowers power if necessary to keep at least a weak signal on the air.
The automation system duplicates what a human would do at the site, automatically handling antenna switching, pattern change, parameter monitoring and other functions. It also performs data logging per FCC guidelines, with this information available remotely. The PLC has a built-in webserver, so we can access logged data remotely via any browser. In our case, this is done through a Cisco firewall at the site.
PLCs have been very reliable compared to the custom control systems used previously. The PLC controls a wide variety of off-the-shelf audio switchers made by various companies. For the radio antenna switching, the PLC is controlling large RF contactors. We control these devices by mixing and matching the PLC’s input and output modules including discrete, analog, relay contact and serial I/O. Using these I/O points, we can interface the PLC to all of our broadcast industry equipment.
We also installed a C-more touch panel display (Figure 3), and created a main screen with buttons to change modes of operation or select a transmitter. The main screen also displays current time and transfer times for the month, along with a wide variety of analog parameters such as transmitter output, current to the antenna and system status. And if needed, a calibration screen can be accessed to scale the analog values to actual engineering units.
Test, Installation and Startup
Installation and startup of the antenna/transmitter automation system took significant planning to minimize the impact on broadcasts. Several test jigs were built to verify operation of the automation system prior to installation, with simulated transmitters built to our specifications to make the test as close to the actual installation as possible.
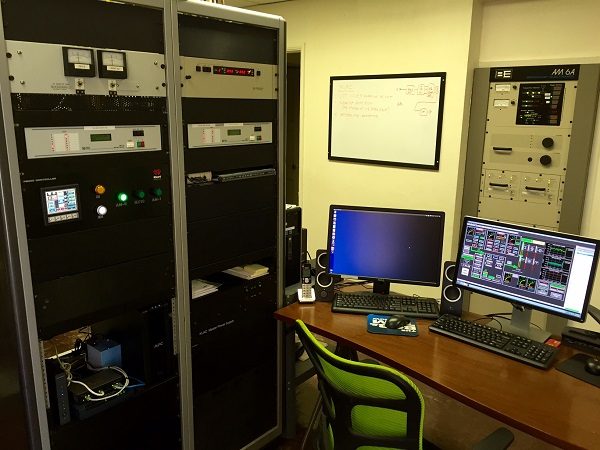
An AutomationDirect C-more touch panel display provides functional information about the transmitter site, as well as manual control and calibration functions.
For testing, we plugged in three simulated transmitters and connected RF contactors. We simulated the complete KLAC setup that the PLC would be controlling, and performed weeks of testing. After some tweaking and optimizing of the PLC and C-more programs, the resulting automation system worked far better than anything that had been installed at KLAC.
The installation went as planned. There were over 30 cables to install, and we used AutomationDirect ZIPLink modules to greatly reduce wiring time. To reduce off-air time to the absolute minimum, signals were bypassed with jumpers until tested so the station could continue transmitting while we installed the new automation system.
There were a few minor tweaks required to the program during onsite startup. When switching transmitter patterns from day to night, the RF signal from the transmitter must be muted to avoid putting 50,000 W through a contactor and damaging it. Tweaking was required to minimize the time that the station was off the air when switching. Actuation times of contactors and RF power-off delay of transmitters needed to be fine-tuned, and when this was completed the pattern switching was barely audible.
Working with AutomationDirect was straightforward and simple. They were chosen based on cost, quick delivery and ease of use. Shipping is free, and they provide emailed status updates. We have called for technical support a few times and were always provided with quick and comprehensive answers.
The AutomationDirect automation system is operating flawlessly at a high-power facility in a remote location. In the future, we plan to use AutomationDirect hardware to automate many more broadcast systems including automatic FM antenna switching, power control, and transmission line pressurization and fault detection.
By: Dennis Sloatman, Vice President of Engineering and Information Technology at iHeartMedia, Los Angeles
Figures all courtesy of iHeartMedia
This article reprinted from NASA Tech Briefs, 2017