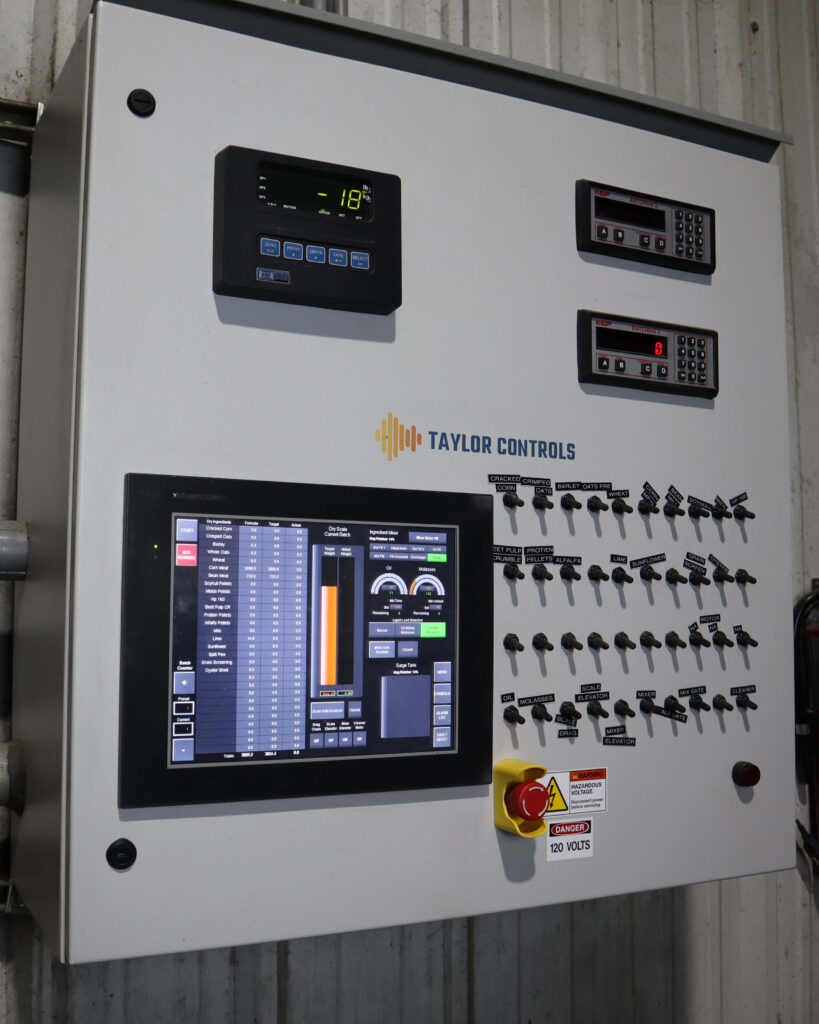
To improve performance and reliability, this grain blending company knew it needed to upgrade its homebrew controls to a modern control system platform.
Many small- and mid-sized manufacturing operations have some degree of automated equipment, but lack the in-house skill to perform upgrades and capital projects. Ethan Taylor founded Taylor Controls to help this market segment, exemplified by a recent project to update the automation system for a grain blending company. He details the work and results in the Design World January 2024 article titled Feeding Time: HMIs and PLCs Help in Grain Blending Application.
Revising the Recipe
The grain production company batches and blends ingredients to produce a variety of livestock feed, and they had designed most of the equipment and electrical/electronic automation systems in-house over the years. However, recipe changeovers still required significant manual effort, and the existing semi-automated system was beginning to exhibit other problems.
To improve reliability, throughput, and safety, the company knew they needed to modernize, so they reached out to systems integrator (SI) Taylor Controls. The SI was experienced in these types of projects, and they worked with the grain production company client to understand the existing operation and expected requirements, as well as some desired upgrades.
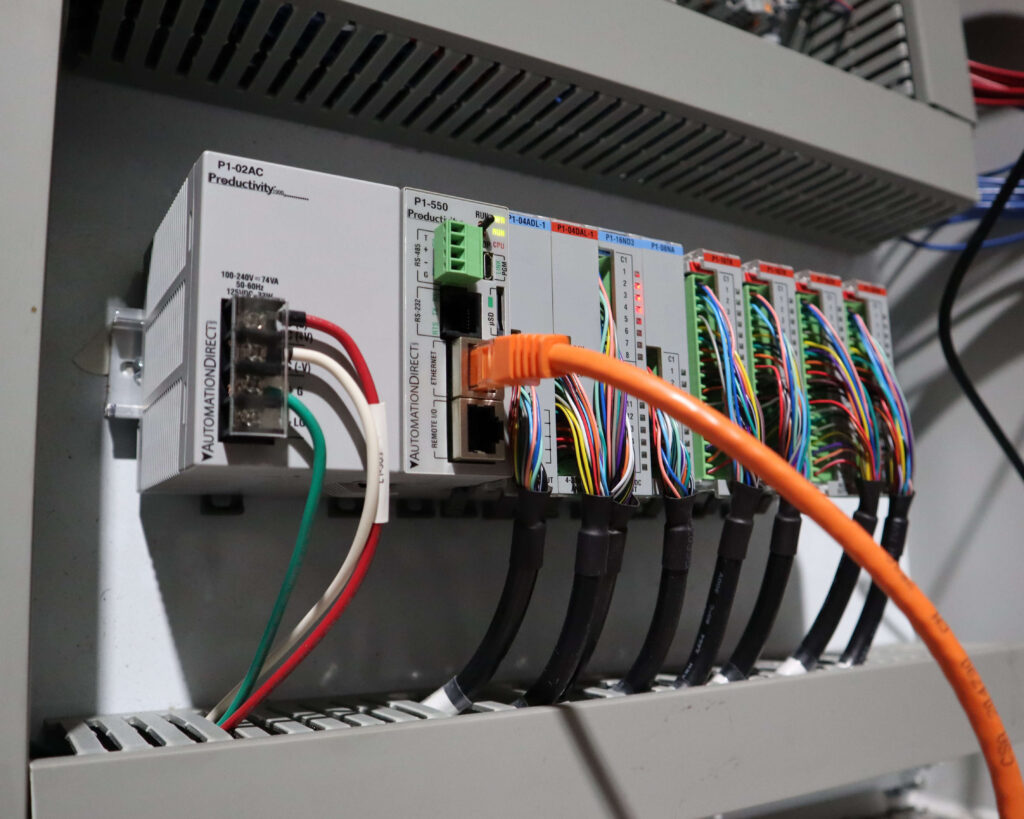
The system uses motor-driven augers to individually feed ingredients into a scaled hopper, first at a fast/bulk speed, but then shifting to a slow/dribble speed to make an accurate weighment.
The existing system did not have any self-learning provisions. Because the material behavior through a feeder could vary greatly depending on the type, quality, and moisture content of each component, the actual weighments fluctuated from target by an unacceptable amount, sometimes from batch to batch. The company desired a dynamic and responsive method to overcome this.
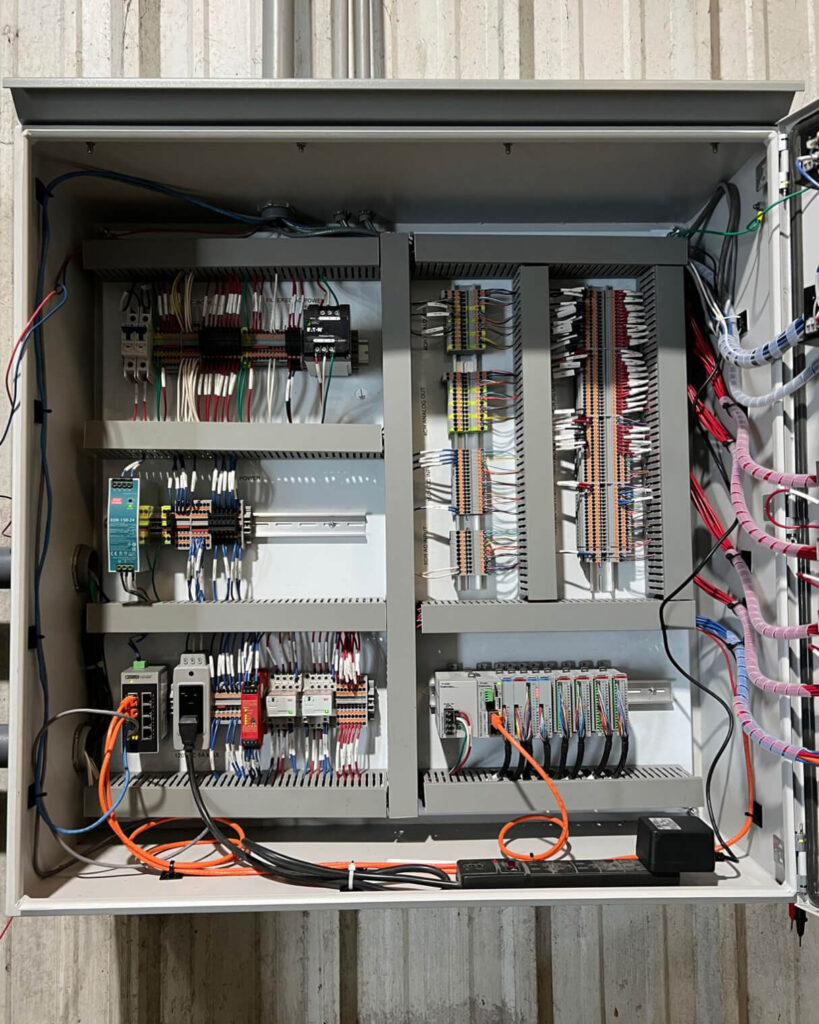
Formulating the Design
Based on many previous positive experiences with AutomationDirect, the team began the design using:
Only one VFD was needed because contactors with properly sized overloads were used to select the active motor. The control panel design came together quickly, with almost all parts sourced from AutomationDirect. The compact Productivity1000 was a good fit for the available space, and it performed all calculations, command of the VFD via EtherNet/IP, and the remainder of control using wired I/O.
Fashioning Flexibility
The new system supports up to 30 ingredients per batch, although only 19 ingredients were initially implemented. Users can easily change active recipes, formulations, and default free fall amounts using the HMI. They can view the operating status, and the system self-adjusts to maintain accuracy. Modular code, and the ability to add remote monitoring and other capabilities, means this system is future-proof and ready for expansion.
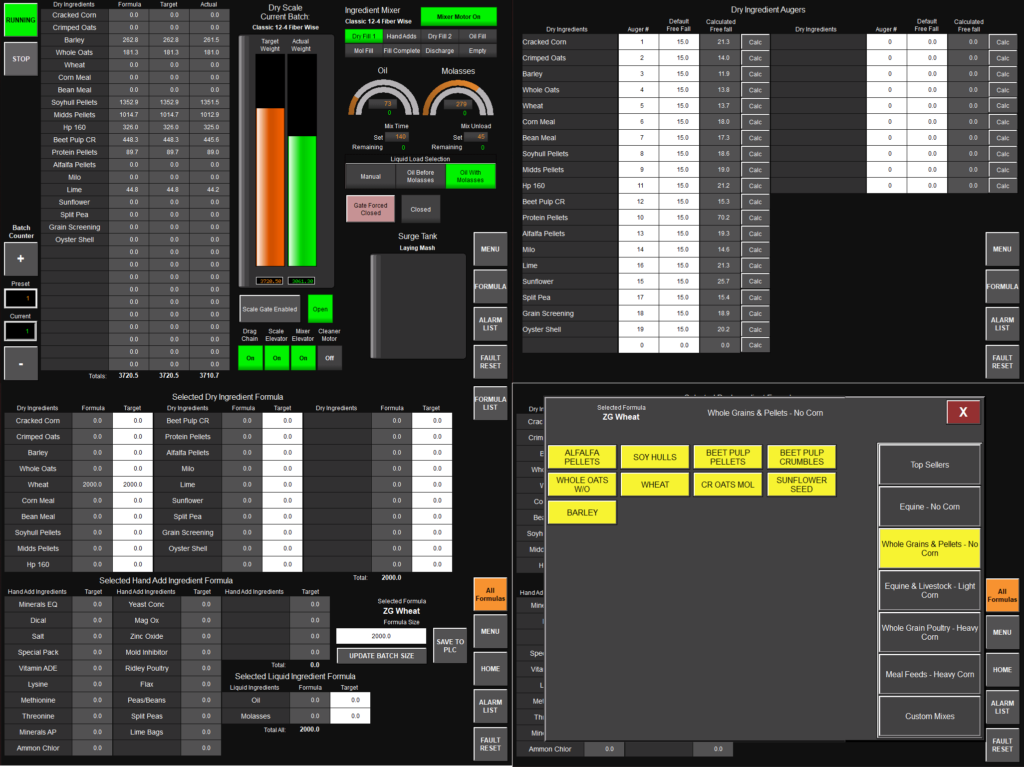
The grain blending company is exceptionally pleased with their new system, which is reliably delivering nimble and accurate batching production. It has also reduced costs by minimizing waste and overshoots, and by speeding up batching rates. Throughput is so high that the blending system can now support addition of another downstream bagger and palletizer.
Visit the AutomationDirect.com website today to explore a range of automation products to help your company modernize operation.
All figures courtesy of Taylor Controls