Using AutomationDirect hardware and software, this company self-performed automation work to meet their needs and ready their team for the future.
At Nehemiah Manufacturing in Cincinnati, OH, the core work is producing consumer products such as detergents and cleaners, but the company also supports the community by employing those who need a second chance. Writing for the February 2020 issue of Machine Design, plant engineer and EHS manager Greg Freeman explains how they achieved both of these goals in an article titled Industrial Automation with a Mission. Here’s a summary, click on the link above for the full text.
When the company outgrew the original facilities, a move provided the opportunity to take a fresh look at improving their industrial automation systems.
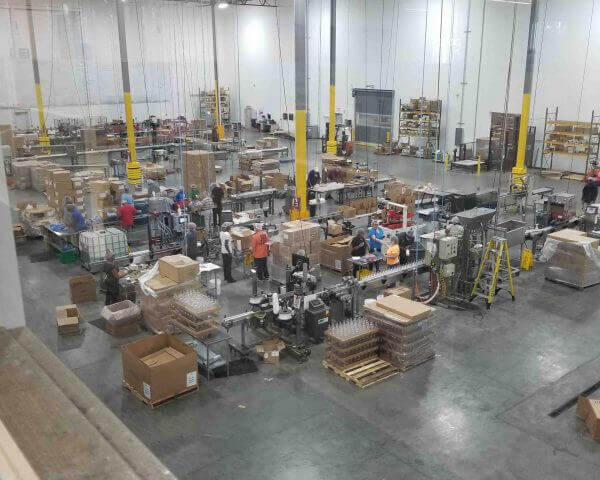
Like many manufacturers, they used a wide variety and vintage of production and packing equipment operating largely as islands of automation, making it a challenge to operate and maintain it all as a cohesive whole.
Taking the First Step
After some initial research, the team determined AutomationDirect hardware and software products would meet their technical needs. The proof-of-concept would be a wastewater treatment skid, which needed programmable logic controller (PLC) and human-machine interface (HMI) automation to monitor and treat the system pH, and report on the same.
Designing In-House
By creating the system design in-house, the team realized many benefits:
- Product standardization makes it easier to support
- Common programming practices and look/feel aids operations and maintenance personnel
- Future modifications and additions, like remote access, are possible
- Proprietary systems avoided
- Plant-wide integration enabled
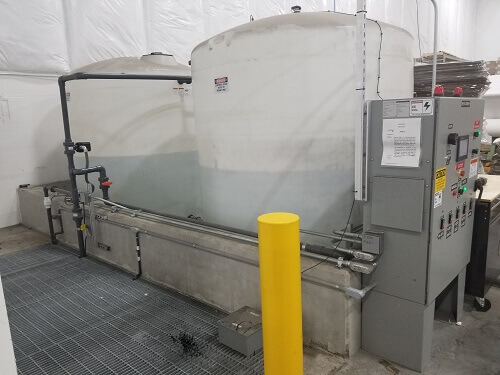
Getting to Work
The Nehemiah team include a plant engineer with a background in process plant automation, and they knew they could engage systems integrators as needed. They found AutomationDirect products ideal for the task because of:
- Comprehensive portfolio of PLCs and HMIs
- Easy-to-use products
- Online product selection tools
- Readily available documentation, including AutoCAD drawings
- Complementary products such as power supplies, relays, and variable frequency drives
- Free or inexpensive software
- Online videos
- Friendly technical support
The team has used CLICK series PLCs, and more recently has standardized on Productivity1000 stackable micro and Productivity2000 micro-modular PLC families. Combined with C-more EA9 series Touch Panel HMIs, they were confident they had a solution which could be deployed in any area.
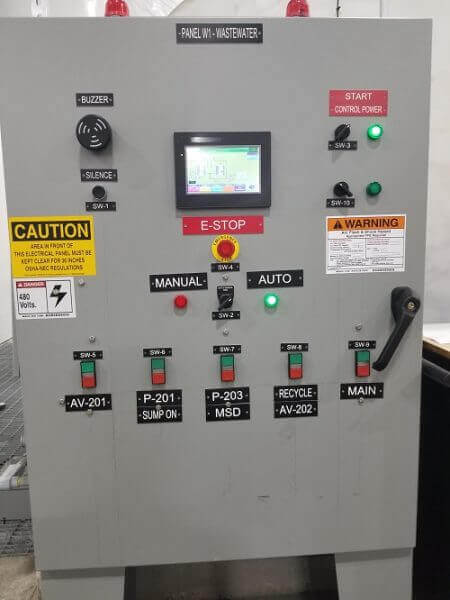
Answers Online
Comprehensive online documentation, including AutoCAD drawings, helped the team create control panel drawings, bills of materials, and operations & maintenance manuals. They found online videos useful for learning various programming and configuration details, which helped to continually improve their confidence in the work.
HMI
While much of the PLC programming effort is behind the scenes, the HMI is the highly visible operator’s window into equipment operation. Because Nehemiah self-performed the work, they could tailor the HMIs to provide the exact experience they wanted, and to ensure the system could be scaled up for consistent plantwide operations. Remote and mobile access allows the team to respond quickly and engage off-site support as needed.
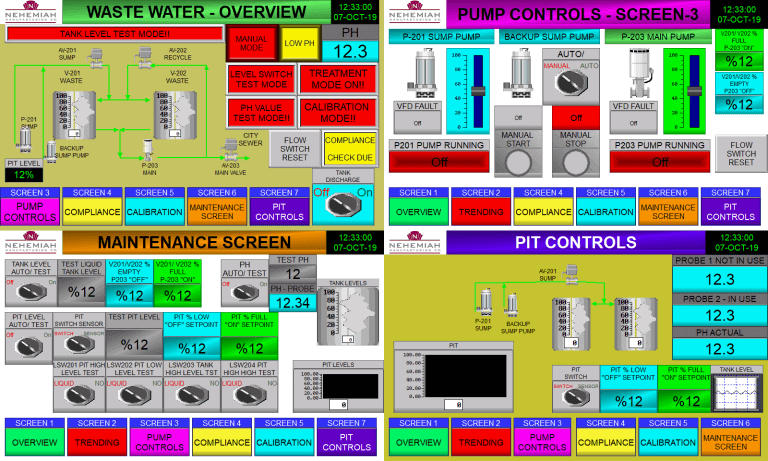
Built for the Future
AutomationDirect helped Nehemiah take charge of their industrial automation future.
Nehemiah found success with its initial automation project, developing the hardware, PLC code and HMI graphics in-house. The system has performed exceptionally with zero downtime or failures. Even if an issue occurs, the team is confident it can quickly troubleshoot, solve the issue and obtain parts quickly.
Based on their great experience, Nehemiah has continued automating other processes, expanded their team training, and look to the future with self-assurance.
Read more application stories here!
Originally Published: March 2020